Aluminum nitride ceramic is an important heat dissipation substrate material, but the aluminum nitride ceramic substrate itself does not have electrical conductivity, so the surface must be metallized before being used as a high-power heat dissipation substrate.
The wetting ability of metal on ceramic surface at high temperature determines the binding force between metal and ceramic, and good binding force is an important guarantee for the stability of packaging performance. Therefore, the realization of metallization of ceramic substrate is an important part of the practical application of aluminum nitride ceramics.
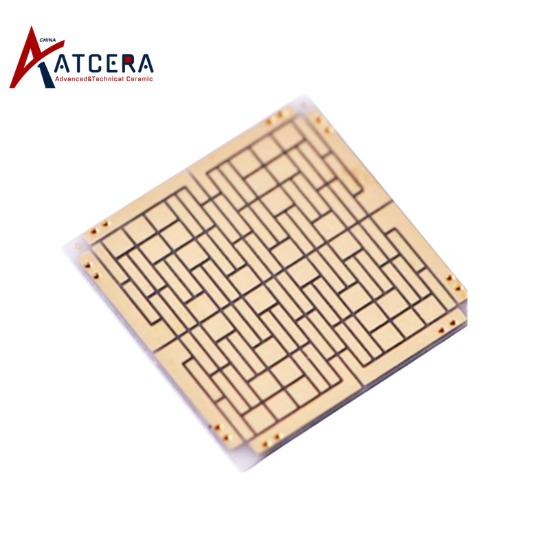
Mechanical Connection and Bonding
The mechanical connection method is characterized by adopting a reasonable structural design and using mechanical stress to realize the connection between aluminum nitride substrate and metal, such as hot sleeve connection and bolt connection. The mechanical connection method has the characteristics of simple process and good feasibility, but the stress at the connection is large, and it is not suitable for high temperature environment and the application range is limited.
Bonding refers to the organic binder as the connection medium, through the appropriate bonding process, the nature of the aluminum nitride substrate and metal materials combined into a mechanical whole connection method. However, the bonding method is also not suitable for high temperature and high strength environment, and the use range is small.
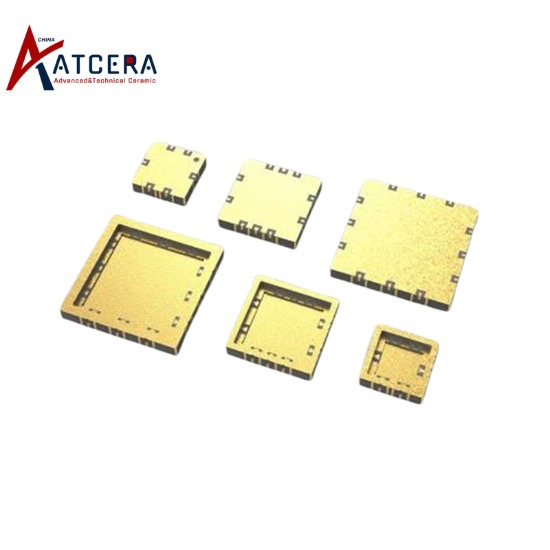
Thick Film Method (TPC)
Thick film method refers to the process of directly coating a conductive paste on the surface of aluminum nitride ceramic substrate through screen printing, and then drying and sintering at high temperature to make the metal coating adhere to the surface of the ceramic substrate.
Conductive paste is generally composed of conductive metal powder, glass binder and organic carrier. The conductive metal powder determines the electrical and mechanical properties of the paste after film formation, and the commonly used metal powders are silver, copper, nickel and aluminum, etc., of which silver and copper have low resistance and low cost, and are more suitable for industrial production.
Therefore, the process is reliable, has the advantages of high production efficiency, low cost and flexible design. Its disadvantage is that it is limited by the precision of the screen printing process, the adhesion is not easy to control, and the sintered substrate can not obtain high-precision lines, so it can only be applied to electronic device packaging materials with low line accuracy requirements.
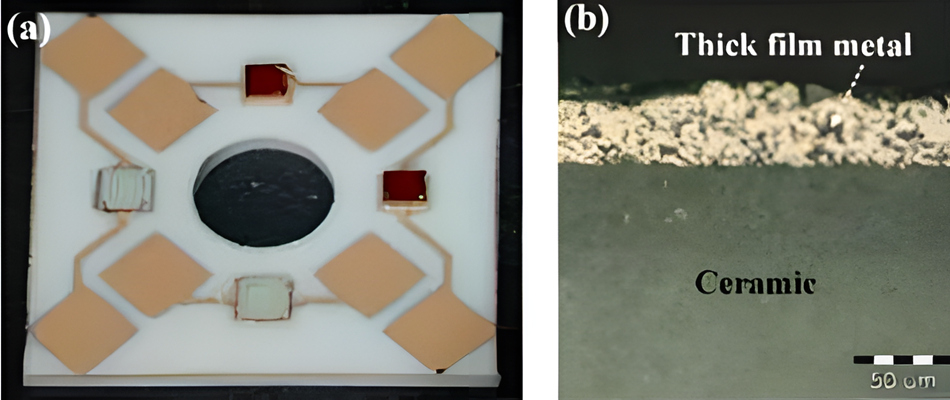
Active Metal Brazing (AMB)
The active metal brazing method is to directly add Ti, Zr, Al, Nb, V and other transition elements with relatively active chemical properties into the common brazing metal. These active elements react chemically directly with the surface of aluminum nitride ceramics to form a transition layer, the main product of the transition layer is some metal bonding compounds, and has the same structure as the metal, so it can be wetted by the melted filler metal to form a metallurgical joint.
Aluminum nitride ceramic substrate is an important heat dissipation device, often used at high temperatures, so more high-temperature joints are needed. The high temperature active brazing metal mainly composed of CuTi and NiTi can be used in the range of 1200~1800℃. Ternary system or multicomponent system brazing metal represented by Au base, Co base and PD-base brazing metal is the most commonly used high temperature active brazing metal. The melting point of Au, Co and Pd is 1064℃, 1492℃ and 1554℃ respectively, which plays a role in increasing the melting point in brazing metal.
Due to the active elements in the brazing metal are chemically active, in order to avoid chemical reactions with oxygen at high temperatures, active brazing must be carried out under the protection of a harsh vacuum environment or an inert atmosphere, and the technical cost is high, and it is not suitable for large-scale applications.
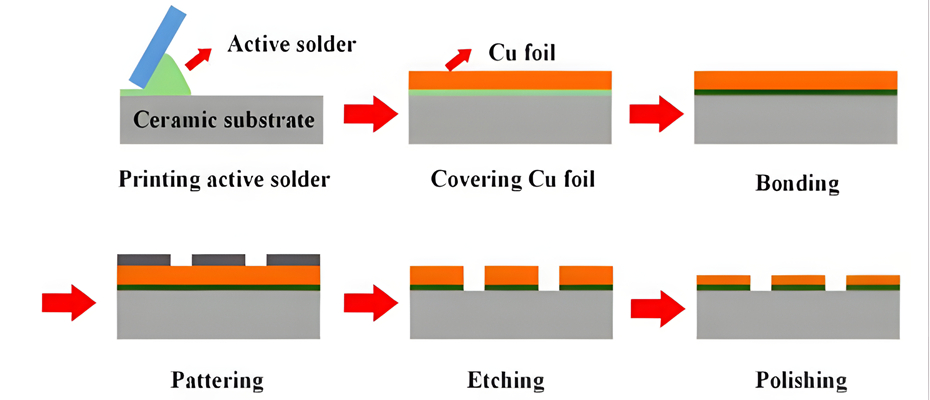