In the field of microelectronic packaging, aluminum nitride ceramics are gradually becoming the preferred material for high-performance chip cooling substrates due to their excellent thermal conductivity, mechanical strength and electrical properties. However, its high hardness and high brittleness can easily cause surface micro-cracks and sub-surface damage during processing, which directly affect the final properties and application effects of the material. Therefore, how to optimize the chemical mechanical polishing (CMP) process of aluminum nitride ceramics to effectively reduce or eliminate these processing defects has become a hot and difficult point in current research.
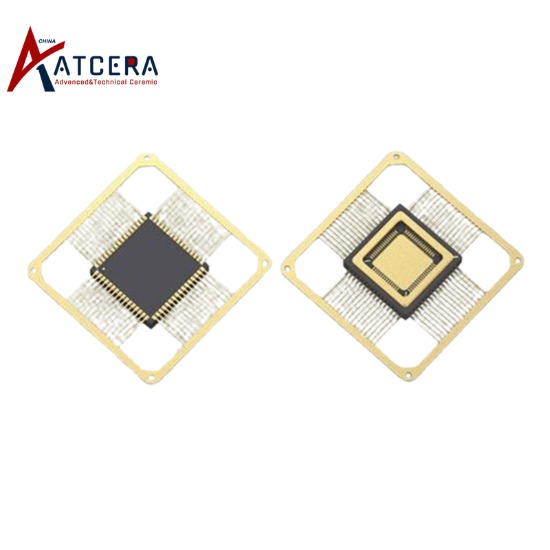
Aluminum nitride ceramics, as a high-performance advanced material, with its excellent thermal conductivity efficiency (thermal conductivity up to about 200-300 W/m·K, far exceeding traditional ceramic materials), excellent mechanical properties (high hardness, high strength), excellent corrosion resistance, as well as good electrical insulation and weldability characteristics, It has shown great potential in the field of microelectronics, especially in the cooling substrate and packaging materials of large-scale integrated circuits (ics). AlN substrate’s lightweight design not only effectively reduces the volume and weight of electronic devices, but also significantly reduces thermal resistance through its ultra-smooth surface (ideal surface roughness Ra ≤ 8 nm, and even requires surface accuracy RMS < 2 nm after polishing), optimizing the heat dissipation efficiency of the chip, which is crucial to improving the overall performance and reliability of integrated circuits.
However, the high hardness (Mohs hardness of about 9), high brittleness and relatively low fracture toughness of aluminum nitride ceramics pose great challenges for precision machining, especially surface flattening. In the process of processing, it is easy to produce surface scratches, micro-cracks and other defects as well as difficult to detect sub-surface damage, which will directly affect the performance and service life of the material. Therefore, how to achieve efficient and high-quality aluminum nitride ceramic surface flattening processing and reduce processing defects has become a key problem to be solved in the field of materials science and engineering.
The core of the chemical mechanical polishing process of aluminum nitride ceramics is to realize the fine processing and flat treatment of the material surface through the dual action of chemical corrosion and mechanical friction. This process can not only significantly improve the surface roughness of the material, but also adjust the surface stress state of the material to a certain extent, so as to improve the overall performance. However, the traditional CMP process is often difficult to balance the processing efficiency and surface quality when processing aluminum nitride ceramics, especially in the prevention of micro-cracks and sub-surface damage.
It is worth noting that compared with more mature semiconductor materials such as silicon carbide, there are still some research gaps in the selection of abrasives, the types of polishing pads and the optimization process of aluminum nitride ceramics in CMP process. In the future, with the in-depth understanding of the characteristics of aluminum nitride ceramic materials and the continuous innovation of CMP technology, it is expected to develop a more efficient, environmentally friendly and suitable for aluminum nitride ceramics CMP process system, and further promote its wide application in the field of high-performance electronic packaging.
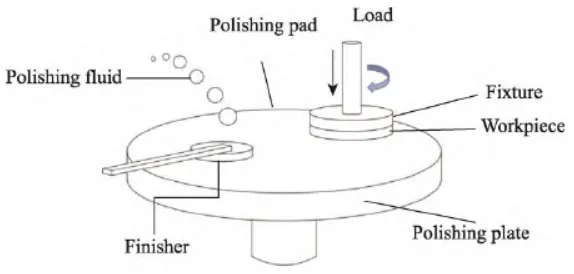
To solve the problem that the surface of aluminum nitride after processing is prone to micro-cracks and sub-surface damage, it is necessary to start from many aspects:
1. Optimize the formulation of polishing fluid: Develop polishing fluid with higher selectivity, which can more effectively remove the surface of the material without damaging its internal structure. At the same time, the pH value, concentration and additive types of the polishing liquid are adjusted to reduce the chemical erosion of aluminum nitride ceramics and reduce the risk of micro-cracks.
2. Improve the selection of polishing pads and abrasives: select polishing pads with moderate hardness and good wear resistance, as well as abrasive particles with uniform particle size distribution and regular shape to reduce mechanical stress concentration during processing and avoid sub-surface damage.
3. Precise control of polishing parameters: including polishing pressure, rotation speed, polishing time, etc. The reasonable setting of these parameters can directly affect the polishing effect and processing quality. By fine-tuning these parameters, it is possible to minimize surface defects while ensuring processing efficiency.
4. Adopt advanced detection and feedback technology: the online monitoring and feedback system is introduced in the CMP process to detect the quality of the machined surface in real time, and adjust the polishing parameters in time according to the feedback results to realize the intelligent and fine control of the processing process.
In summary, the optimization and improvement of chemical mechanical polishing process of aluminum nitride ceramics is the key to solve the micro-cracks and sub-surface damage of aluminum nitride surface after processing. Through the comprehensive application of the above strategies, the processing quality and application performance of aluminum nitride ceramics can be significantly improved, and the wide application and development of aluminum nitride ceramics in the field of microelectronics packaging can be promoted.