Si3N4 powder is the main raw material for the preparation of silicon nitride balls. Selecting the appropriate treatment method to obtain the powder with regular shape and uniform particle size distribution is the basis for the stable implementation of Si3N4 ceramic ball forming, sintering, processing and other processes.
According to the different atomization methods, the spray granulation methods of Si3N4 powder mainly include centrifugal spray granulation, pressure spray granulation and two-fluid spray granulation. Pressure spray granulation The slurry with uniform Si3N4 powder is sprayed into the granulation tower under high pressure for atomization, and the droplets are quickly dried into spherical powder by hot air flow, which can prevent the agglomeration and sedimentation of various components in the slurry. By controlling the volatilization rate of the solvent on the surface of the particles, the regular particle morphology can be obtained, and the spray granulation powder with uniform particle size distribution, good fluidity and suitable loose density can be packed. Thus, the performance of the powder filling mold is improved, and the density and uniformity of the blank are increased. Therefore, the pressure spray granulation method was selected to study the effect of the loose density of spray granulation powder on the properties of Si3N4 ceramic balls.
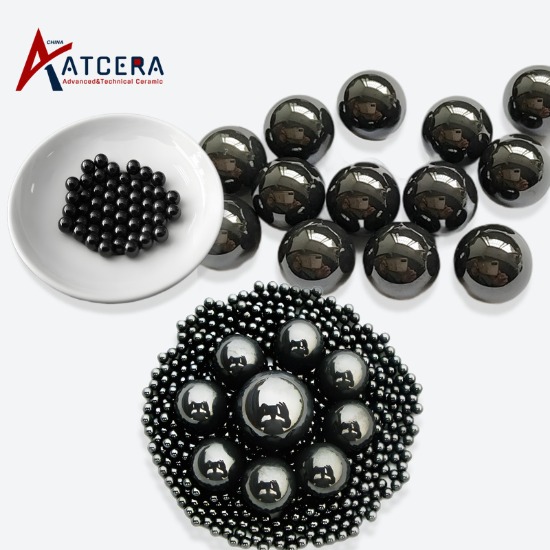
Test Material
Si3N4 powder (when the cumulative volume fraction in the particle size distribution is 50%, the corresponding particle size D50=1.5μm, α-Si3N4 content is 93%, the purity is 99.9%), Y2O3 powder (D50=1.8μm, the purity is 99.9%), Al2O3 powder (D50=2.2μm, the purity is 99.95%), etc.
Sample preparation
According to Si3N4∶Y2O3∶Al2O3= 92%∶4%∶4%(mass ratio), the mixture was added to the ball mill, anhydrous ethanol was used as the solvent, Si3N4 ball was used as the grinding medium for mixing and dispersing, mixing time was 24h, the mass ratio of Si3N4 ball and mixed powder was 3:1. After uniform mixing, the mass fraction of solid phase of the slurry is 55%, and the viscosity is 4000MPa·s. By controlling the inlet temperature of the spray drying tower and the diameter of the spray plate, the granulated powder with different loose density was obtained. The Si3N4 spray granulation powder was pressed into a ceramic pellet with a diameter of 8.731mm by a dry press, and then the atmosphere pressure sintering was carried out at 1850℃, the heating rate was 3℃ /min, the holding time was 1.5h, and the nitrogen pressure was 9MPa. The properties were tested after preparation.
Result
The screening fraction data and loose density of the granulated powder prepared by different spray granulation processes with the same batch slurry are shown in Table 1. The density of ceramic pellet blank, sintering density, bending strength, crushing load, fracture toughness and Vickers hardness of the ceramic pellet pressed by spray granulation powder with different loose density are shown in Table 2.
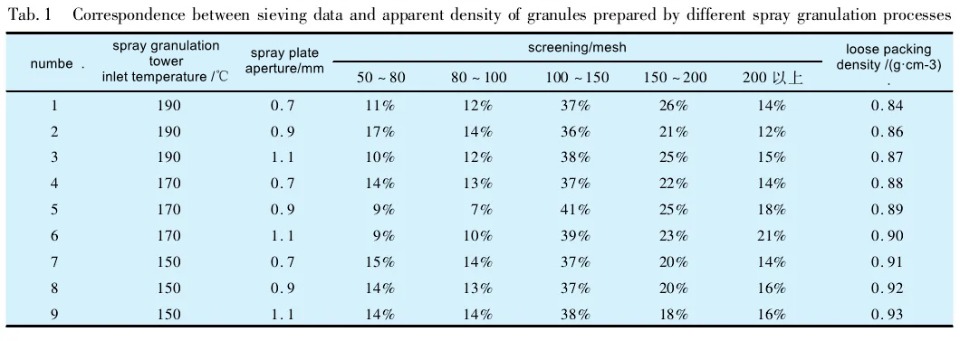
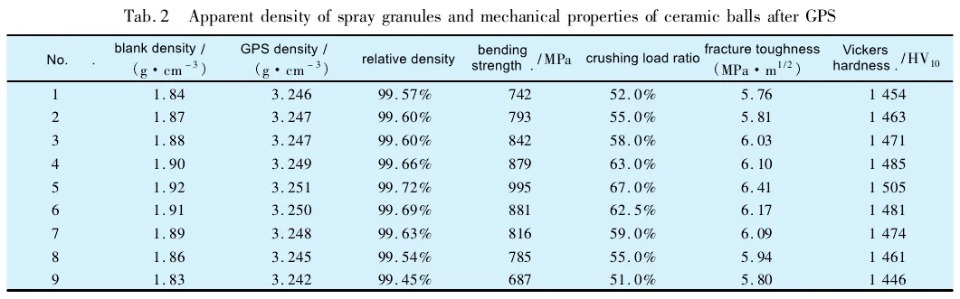
The mechanical properties of Si3N4 ceramic ball pressed by 5# granulated powder are the best. Too high or too low loose density will affect the pressing performance of the powder and the density of Si3N4 ceramic ball blanks, thus affecting the mechanical properties of Si3N4 ceramic balls. The mechanism is that the loose density directly affects the porosity of the spray granulation powder after pressing, and the gas is difficult to discharge, resulting in the long migration distance of particles and substances during the sintering process, which is not conducive to sintering densification.
The particle morphology of the 5# Si3N4 spray granulation powder is solid and spherical (Figure 1).
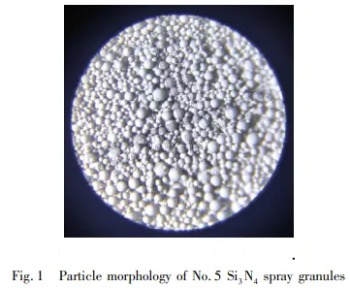
The microstructure of Si3N4 ceramic ball GPS by 1# ~ 9# spray granulation powder is shown in Figure 2. With the increase of loose density of granulation powder, the number of pores inside Si3N4 ceramic ball after GPS first increases and then decreases, and the density of Si3N4 ceramic ball first increases and then decreases.
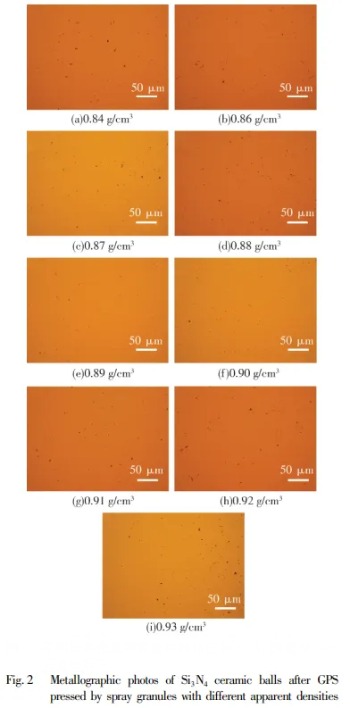
SEM was used to observe the microstructure and grain fracture morphology of the crushed samples of Si3N4 ceramic balls with the best mechanical properties and poor mechanical properties. As shown in Figure 3, the density of Si3N4 ceramic balls first increased and then decreased with the increase of loose density of granulated powder. Too high or too low loose density would lead to uneven grain growth and internal pores.
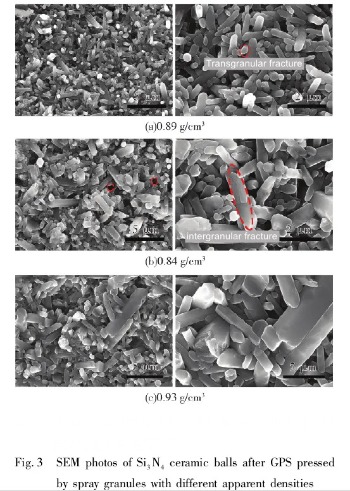
Conclusion
With Si3N4 powder as raw material and Y2O3 and Al2O3 as sintering additives, the influence of loose density of spray granulation powder on densification and mechanical properties of ceramic ball sintering was analyzed. The following conclusions were drawn:
1) The density of Si3N4 ceramic ball blank increases first and then decreases with the increase of the bulk density of granulated powder. When the loose packing density is 0.89g /cm3, the Si3N4 ceramic ball has the highest densification degree and the best mechanical properties.
2) When the bulk density of spray granulation powder is 0.89g /cm3, the formed Si3N4 ceramic ball has the smallest pores, uniform grain size, and mainly adopts the mode of transgranular fracture.