In the realm of advanced materials, ceramic crucibles for melting stand as a testament to the integration of cutting-edge technology and traditional craftsmanship. As the industrial landscape evolves, the demand for specialized, high-performance crucibles has increased, particularly in Europe and the Americas. This article delves into the intricacies of ceramic crucibles for melting, their unique characteristics, applications, selection criteria, manufacturing process, and real-world case studies.
Characteristics of Ceramic Crucibles for Melting
Ceramic crucibles for melting are crafted from high-purity, ultra-fine inorganic compound powders. These materials undergo rigorous manufacturing techniques and structural design to yield crucibles that exhibit unmatched properties. Key among these are their exceptional thermal stability, resistance to chemical corrosion, and superior durability. Additionally, ceramic crucibles boast minimal heat loss, ensuring efficient energy utilization and cost savings.
Application Fields of Ceramic Crucibles for Melting
The versatility of ceramic crucibles for melting has led to their widespread adoption across various industries. In the metallurgy sector, they are employed for the melting of precious metals and alloys, owing to their ability to withstand extreme temperatures without degradation. Similarly, in the glassmaking industry, ceramic crucibles are preferred for their chemical inertness and ability to maintain purity during the melting process. Furthermore, they find applications in the semiconductor industry for the precise melting of materials required for chip fabrication.
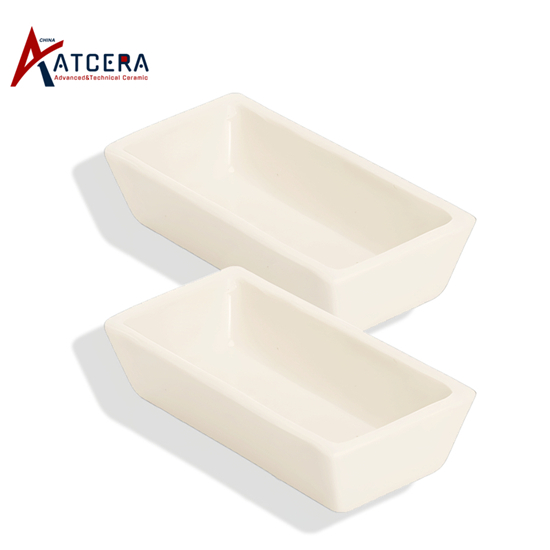
How to Select the Right Ceramic Crucible for Your Project
Choosing the appropriate ceramic crucible for your specific application is crucial. Factors such as the melting temperature required, the material being melted, and the desired crucible lifetime should be considered. Additionally, the crucible's compatibility with the melting environment and any specific requirements for heat retention or dissipation should be taken into account. By understanding these parameters, one can ensure the selection of a ceramic crucible that meets the project's needs and optimizes performance.
Manufacturing Process of Ceramic Crucibles for Melting
The manufacturing process of ceramic crucibles for melting is a highly specialized and intricate one. It begins with the selection of high-grade raw materials, by precise powder processing techniques to achieve the desired chemical composition and particle size. The powder is then shaped into the crucible's desired form using advanced molding methods. The crucible undergoes rigorous sintering and firing processes to achieve the required density, strength, and porosity. Finally, a series of quality checks ensures that each crucible meets stringent performance standards.
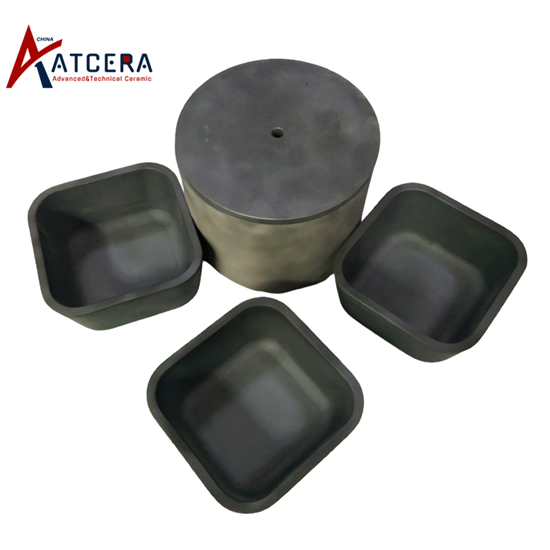
Case Studies and Success Stories of Using Ceramic Crucibles for Melting
Numerous case studies and success stories highlight the benefits of using ceramic crucibles for melting. One such instance involves a leading metallurgy firm that replaced its traditional crucibles with ceramic crucibles. The switch resulted in significant improvements in energy efficiency, material purity, and crucible lifetime, leading to substantial cost savings and a boost in productivity. Similarly, a glassmaking company utilizing ceramic crucibles has achieved higher product quality and reduced waste, further strengthening its position in the market.
Conclusion
Ceramic crucibles for melting are a testament to the convergence of tradition and technology. Their unique properties and versatility have made them indispensable in various industries, particularly in Europe and the Americas. By understanding their characteristics, applications, and selection criteria, one can unlock their full potential and harness their benefits for specific projects. As the industrial landscape continues to evolve, ceramic crucibles for melting will remain a critical component in driving innovation and efficiency.