In the rapidly developing electronics industry, alumina substrate has become an indispensable substrate for electronic components with its excellent insulation properties, chemical stability, high thermal conductivity and good high-frequency characteristics. It not only provides support for electronic components, but also plays a key role in heat dissipation and insulation. However, the preparation process of high quality alumina ceramic substrate is complex and fine. The key factors such as raw material formula, casting film thickness and sintering process parameters directly affect the thickness uniformity, appearance quality and surface roughness of the product, and then determine the overall performance of the product. In this article, the effects of three key additives, binder, plasticizer and dispersant, and their process control were discussed in order to provide reference for optimizing the preparation process of alumina ceramic substrate.
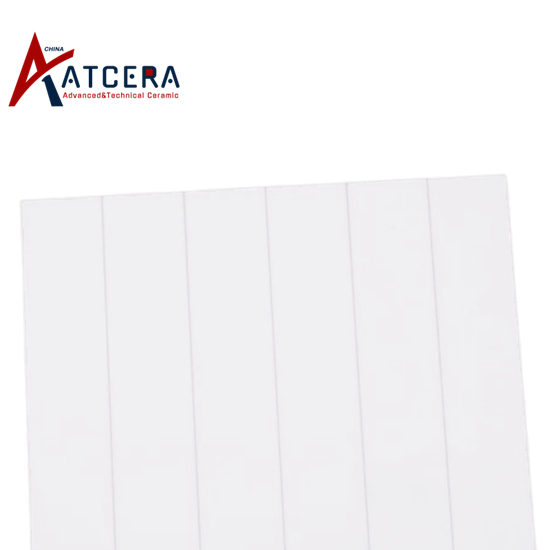
Selection of binder and control of additive amount
As a key organic additive for the construction of three-dimensional networks of ceramic sheets, binders must be soluble in selected solvents, and common types include polyethylene, polyvinyl alcohol, etc. The effect of the appearance, processing characteristics and porosity of the casting green billet on the performance of the product should be considered comprehensively when the amount of binder added. The proper amount of binder can ensure the strength and toughness of green billet, but too much binder will lead to the difficulty of degreasing and the decrease of green billet density, which will affect the shrinkage rate and mechanical properties of finished product. Too little can not effectively bond the powder.
Introduction and balance of plasticizers
By reducing the plastic limit temperature of the binder, the plasticizer enhances the flexibility and workability of the cast film, solves the problem of insufficient toughness after drying, and improves the stability of the slurry. However, the addition of plasticizers should be moderate to avoid excessive reduction of film strength. The ideal plasticizer should have stable physicochemical properties that are compatible with other ingredients of the paste, ensuring minimal addition while maintaining performance.
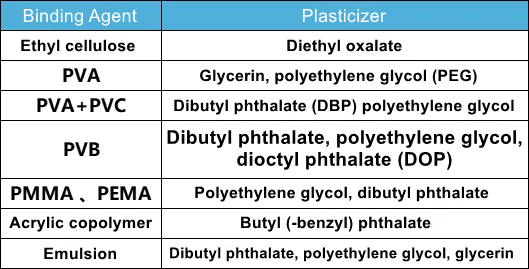
Common binders correspond to plasticizers
Selection and dose adjustment of dispersant
The good dispersion of powder in slurry is the basis of preparing high quality alumina ceramic substrate. The dispersing agent promotes the suspension of particles through electrostatic and steric hindrance and stably disperses. Depending on the slurry system, it is important to choose the right type of dispersant (such as inorganic, organic, polymer and composite dispersant). The amount of dispersant added is adjusted according to the size of the alumina powder, and fine particles usually need more dispersant because of their high surface energy.
In summary, the selection and process control of binder, plasticizer and dispersant have a decisive influence on the performance of the final product during the preparation of alumina ceramic substrate. The thickness uniformity, appearance quality and surface roughness of alumina ceramic substrate can be effectively improved by precisely regulating the types and amounts of these additives, combined with the optimized casting film thickness and desviscose sintering process parameters, so as to ensure its excellent performance in electronic components. In the future, with the continuous progress of material science and preparation technology, further optimization of additive formulation and process parameters will open up new possibilities for the application of alumina ceramic substrates in a wider range of fields.