Zirconia beads find their application in grinding the anode and cathode materials of lithium-ion batteries. Below are three methods for preparing lithium iron phosphate (LiFePO4) using zirconia beads.
Carbothermal Reduction Method
The carbothermal reduction method utilizes the reducing property of carbon to reduce Fe3+ while simultaneously forming a carbon coating on the surface of LiFePO4. This carbon coating prevents particle aggregation, increases inter-particle contact, and improves electrical conductivity. One of its advantages is that it creates a strong reducing atmosphere during synthesis, allowing the use of not only divalent iron compounds but also trivalent iron compounds as iron sources, thus reducing costs. Companies such as Valence in the United States and Suzhou Hengzheng have adopted this method for LiFePO4 preparation. This method offers the advantage of a simple and controllable production process, where a sample can be obtained after a single sintering, providing an alternative route for the industrialization of LiFePO4. Using Fe2O3, Li2CO3, NH4H2PO4, and carbon black as raw materials, LiFePO4/C powders are prepared via the carbothermal reduction method. The LiFePO4/C synthesized under 700°C in an inert atmosphere exhibits excellent crystallinity and a high initial charge-discharge capacity of 150mAh/g. Research on the preparation of lithium iron phosphate cathode materials using iron oxide as the iron source and the carbothermal reduction method has explored the reaction mechanism. In the reaction, Fe2O3 → Fe3O4 → FeO, and FeO reacts with LiH2PO4 at 600°C to form LiFePO4. Using CH3COOLi, NH4H2PO4, Fe(CH3COO)2, and citric acid as raw materials, the desired product is obtained through ball milling, drying, pressing, and sintering. This sample exhibits good electrochemical performance, with an initial discharge capacity of 148mAh/g at 0.2C rate and a capacity loss rate of only 3% after 50 cycles. The effects of three process factors: sintering temperature, sintering time, and carbon content, on electrochemical performance were studied. Through optimized experiments, the best process conditions were found to be 12% carbon content and sintering at 750°C for 15 hours, under which the synthesized sample exhibited the best electrochemical performance, with an initial charge-discharge capacity of 140mAh/g and a capacity retention rate of 97% after 80 cycles.
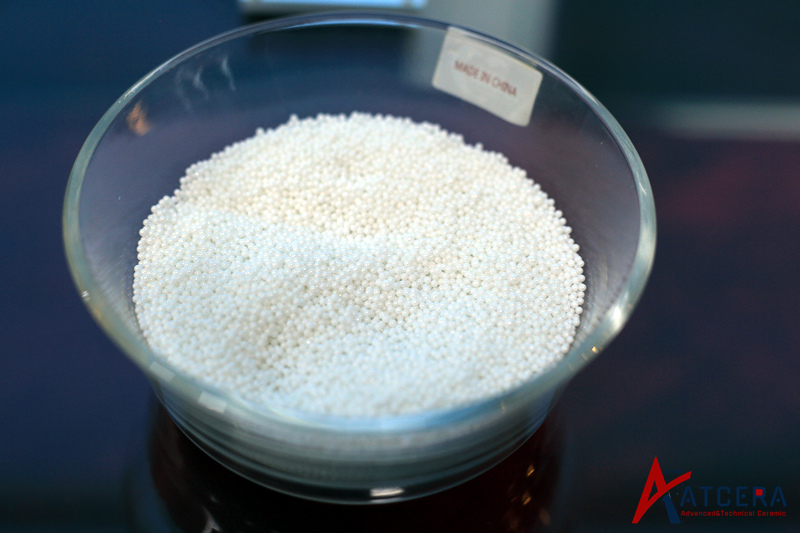
Microwave Sintering Method
The microwave sintering method, characterized by its strong penetrating capability, enables the simultaneous heating of both the surface and the center of an object, achieving uniform heat distribution. Compared to other heating methods, it boasts rapid heating rates, short synthesis times, uniform heating, and low energy consumption. The preparation of LiFePO4 using the microwave method involves ball-milling stoichiometric ratios of Fe(CH3COO)2, Fe(CH2CHOHCOO)2·2H2O, and Fe as iron sources with Li2CO3 and NH4H2PO4 using zirconia beads. After drying and pressing, the samples are placed in crucibles and heated in a household microwave oven. Notably, Fe(CH2CHOHCOO)2 is non-microwave-absorbing and thus does not react. Experimental results indicate that the microwave heating time is a crucial factor in the synthesis of LiFePO4. Samples derived from Fe as the iron source exhibit superior electrochemical performance, with an initial discharge capacity of 125mAh/g at 60°C and 0.1C rate. Using FeC2O4 as the raw material, incorporating 15% graphite powder, and undergoing grinding, pressing, and pre-decomposition, the samples are then placed in a 500W household microwave oven. Analysis of the heating time reveals its impact on the sample's structure and morphology. LiFePO4 begins to form after 5 minutes of heating, but the crystal structure is incomplete and blocky. Heating for 9 minutes results in sharp diffraction peaks, indicating well-developed crystals with the smallest grain size. However, heating for 11 minutes leads to the formation of an impurity phase, Fe3(PO4)2, likely due to decomposition caused by excessive heating. The optimal sample obtained after 9 minutes of microwave heating exhibits a complete crystal structure with the smallest grain size and an initial discharge capacity of 148mAh/g.
Mechanochemical Method
The mechanochemical method is employed to prepare highly dispersed compounds. The application of mechanical force breaks down particles, increasing the contact area and introducing lattice defects, thereby promoting chemical reactions. Utilizing LiOH, FeC2O4, and (NH4)2HPO4 as raw materials, LiFePO4 cathode materials with excellent electrochemical performance are prepared via a mechanical alloying process. Ball-milling Fe3(PO4)2, Li3PO4, and sucrose for 24 hours in a planetary ball mill using zirconia beads, by heat treatment at 500°C for 15 minutes under a nitrogen atmosphere, leads to the synthesis of LiFePO4. The heat-treated LiFePO4 exhibits a complete crystal structure with a conductive carbon additive. Its specific discharge capacity at 0.2C rate is close to the theoretical value of 160mAh/g, demonstrating excellent cycling performance.
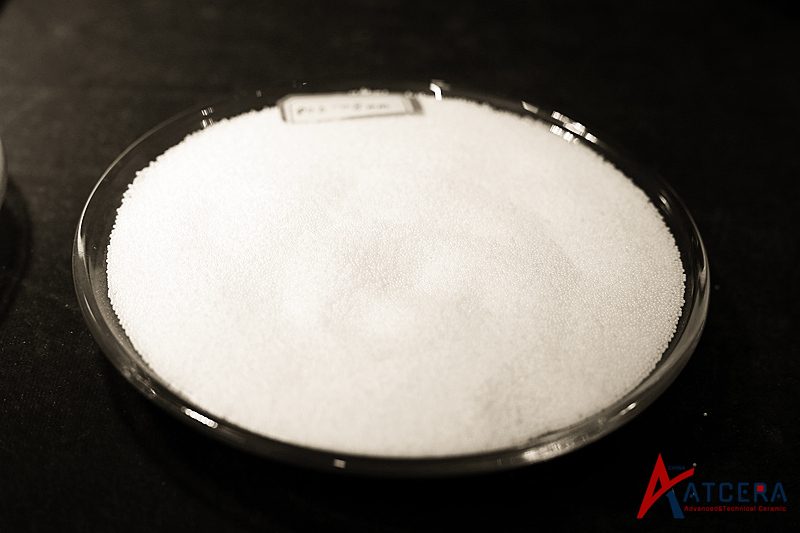
Conclusion
In summary, zirconia beads play a significant role in the grinding process of the anode and cathode materials for lithium batteries, particularly in the preparation of lithium iron phosphate. Their application has enabled three distinct preparation methods—the carbothermal reduction method, microwave sintering method, and mechanochemical method—to achieve remarkable results. By optimizing process parameters, these methods have successfully produced lithium iron phosphate materials with high electrochemical performance, providing strong support for the performance enhancement and industrial production of lithium batteries. With the continuous advancement of technology and further research, it is expected that the application of zirconia beads in the lithium battery field will become more extensive, contributing significantly to the development of the new energy sector.