Zirconia is an inorganic non-metallic material with superior performance and acid-alkali resistance. It boasts stable chemical properties, a high melting point, low thermal conductivity, hardness, high strength, and wear resistance. Due to its remarkable properties, zirconia and its products have become one of the primary raw materials for structural ceramics, functional ceramics, bioceramics, and thermal barrier coatings, exhibiting broad application prospects in high-tech fields such as military, energy, metallurgy, electronics, communications, automotive, and machinery.
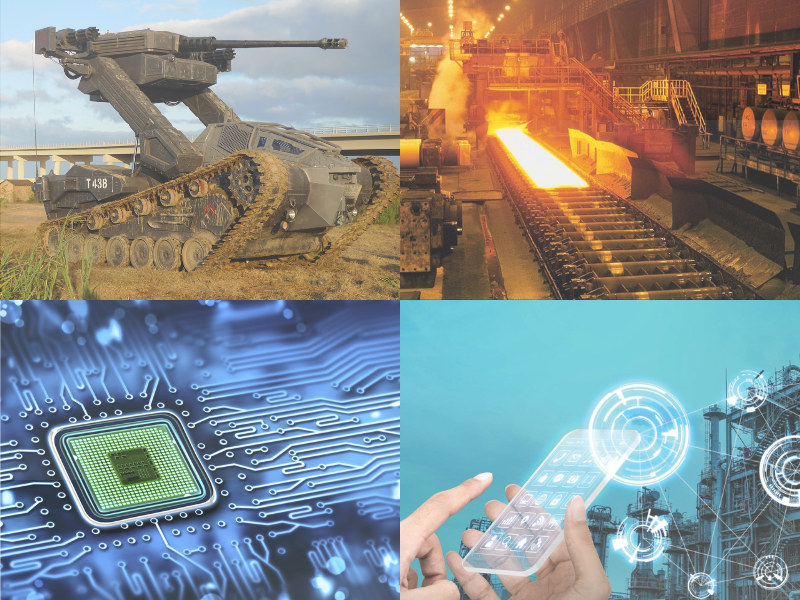
The Application of Zirconia as an Additive in Enhancing the Performance of Other Ceramic Materials
I. Impact on Zirconia Ceramics
Nanozirconia exerts a positive influence on the performance of ordinary zirconia products.
By adding different contents of CaO stabilizer to the electrofused monoclinic zirconia raw material, the optimal amount of CaO stabilizer was determined through analyzing the mineral phase composition, apparent porosity, and compressive strength of the samples after firing. Based on the optimal CaO stabilizer addition, nano-zirconia powder was incorporated to investigate its effect on the performance of zirconia products. The results showed that with increasing nano-zirconia powder addition to the optimal sample (3Ca-PSZ), the apparent porosity decreased, the sintering shrinkage rate increased, and the compressive strength improved. Specifically, when the nano-zirconia powder addition ratio reached 8wt%, the sample exhibited a porosity of 9.4%, a bulk density of 5.08g/cm3, and a compressive strength of 381MPa. Compared with the 3Ca-PSZ sample, the porosity decreased by 40%, the bulk density increased by 5%, and the compressive strength improved by 70%.
II. Impact on Alumina Ceramics
Al2O3 ceramics are widely used in mechanical, electronic, and chemical industries due to their excellent properties such as high strength, hardness, wear resistance, oxidation resistance, and thermal shock resistance. While pure Al2O3 ceramics exhibit good high-temperature performance, they suffer from insufficient toughness and poor impact resistance, often resulting in minor chipping during cutting. By adding zirconia to the Al2O3 matrix, zirconia-toughened alumina (ZTA) ceramics can significantly improve these issues.
In ZTA ceramics, ZrO2 particles are uniformly dispersed in the Al2O3 matrix. As the temperature changes, ZrO2 particles undergo phase transitions, belonging to the martensitic phase transition, resulting in volumetric expansion and shear strain, leading to the formation of tensile stress and microcracks. Some small-sized ZrO2 particles generate microcracks under tensile stress. These cracks are confined within small-sized grains, and their initiation and propagation consume energy from the external stress field, thereby enhancing the toughness and strength of Al2O3 ceramics. Therefore, ZTA ceramics represent a promising ceramic material.
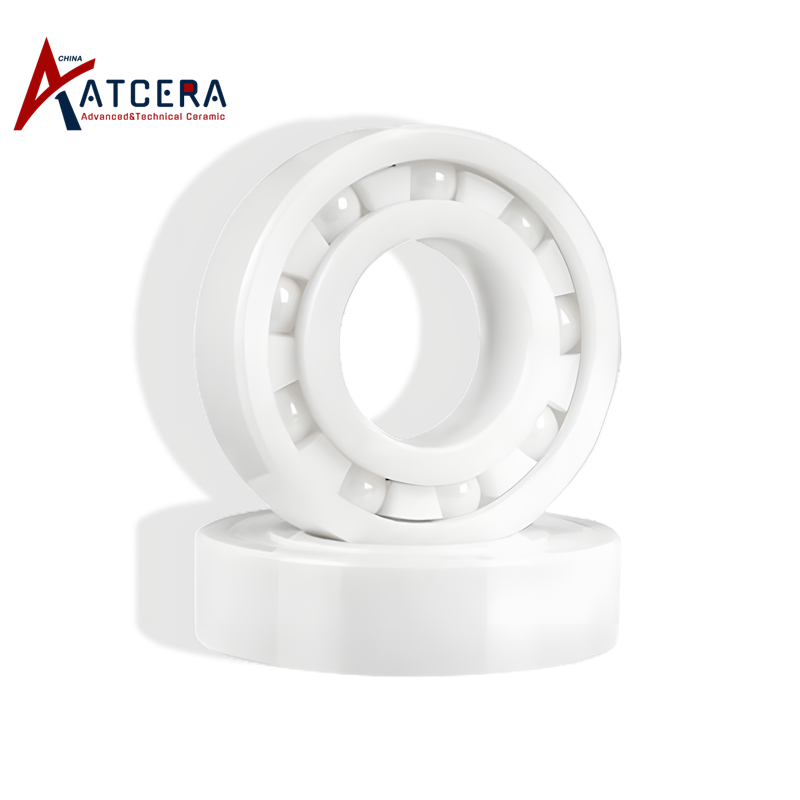
III. Impact on Silicon Nitride Ceramics
Silicon nitride ceramics are considered the most comprehensive structural ceramic material due to their excellent properties such as high strength, hardness, wear resistance, corrosion resistance, and creep resistance. However, their inherent brittleness hinders their widespread market application. Numerous scholars have studied ZrO2-toughened Si3N4 ceramics and made significant progress.
ZrO2-Si3N4 composite ceramic materials were prepared through pressure-less sintering and characterized using the displacement method, SEM, and DDL110 universal tensile testing machine. The influence of ZrO2 content on the density, microstructure, and mechanical properties of Si3N4 ceramics was investigated. The results indicated that as the ZrO2 content increased, the density of Si3N4 ceramics increased; both flexural strength and fracture toughness initially increased and then decreased. When the ZrO2 content reached 10%, the flexural strength and fracture toughness of Si3N4 reached their maximum values simultaneously, being 362MPa and 7.0MPa·m1/2, respectively.
IV. Impact on Aluminum Nitride (AlN) Ceramics
AlN ceramics, renowned for their high thermal conductivity, excellent electrical properties, and low thermal expansion coefficient, are often deemed the ideal material for circuit packaging substrates. However, compared to ceramic materials such as Si3N4 and SiC, AlN ceramics exhibit lower fracture toughness, which compromises their thermal shock resistance and increases the difficulty of machining.
By incorporating nano-ZrO2 powder and utilizing Y2O3 as a sintering aid, AlN ceramics were fabricated through hot-press sintering. The results revealed that the phase composition of the hot-pressed AlN ceramics after adding ZrO2 comprises the primary AlN phase, the Al5Y3O12 grain boundary phase, and a new ZrN phase. With the addition of ZrO2, the Vickers hardness of the hot-pressed AlN ceramics remained largely unchanged, while its fracture toughness gradually improved. This enhancement is primarily attributed to the high-temperature reaction between the added ZrO2 and AlN, resulting in the formation of ZrN. This transformation leads to a shift from a single intergranular fracture mode in AlN ceramics to a mixed fracture mode encompassing both intergranular and transgranular fractures, strengthening the grain boundaries and subsequently improving the fracture toughness.
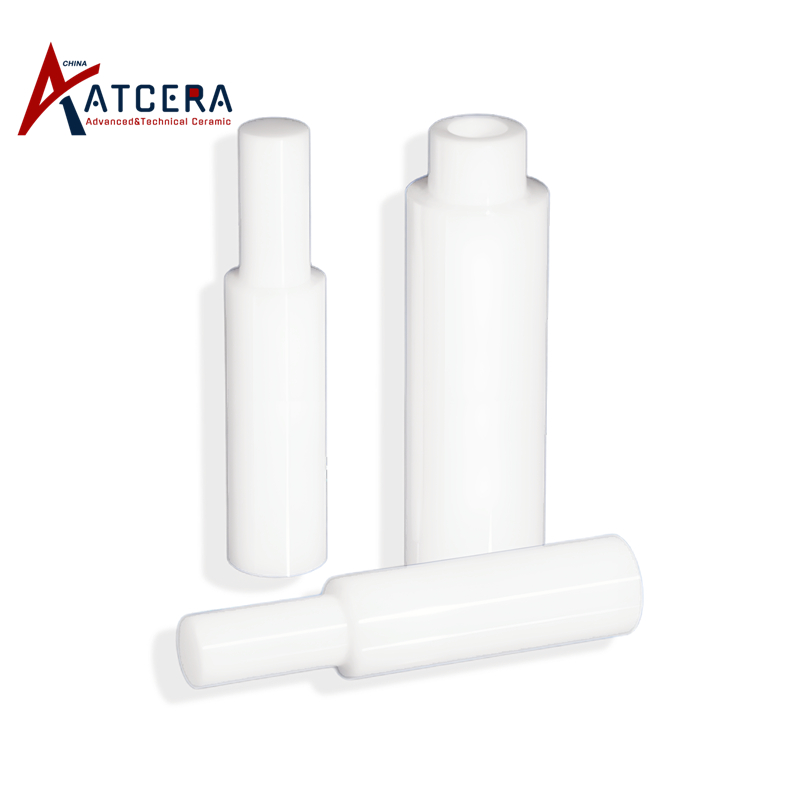
Conclusion
In conclusion, the addition of zirconia significantly enhances the performance of various types of ceramics. Whether it be zirconia ceramics themselves, alumina ceramics, silicon nitride ceramics, or aluminum nitride ceramics, the incorporation of an appropriate amount of zirconia effectively improves key properties such as toughness, strength, impact resistance, wear resistance, and corrosion resistance. This transformation not only enhances the practicality of ceramic materials but also broadens their application scope in high-tech fields like military, energy, metallurgy, electronics, telecommunications, automotive, and machinery. Therefore, zirconia, as an essential ceramic additive, plays a significant role in enhancing the comprehensive performance of ceramic materials.