Brazing is the most important process in the process of AMB silicon nitride substrate, and the preparation of active brazing filler metal and active metal brazing are the key and difficult points at present.
Ti, Zr, Hf, V, Nb, etc. are common active metal elements that can infiltrate silicon nitride substrate surfaces and are widely used for active sealing between ceramics and metals. Among them, the Ag-Cu-Ti alloy with Ti as the active element is the most studied and most widely used active filler metal. It can wet most ceramic surfaces at the temperature of 800~950 ℃, and the brazing head has high strength and stable performance, so that the sealing between ceramics and metals, ceramics and ceramics can be better realized.
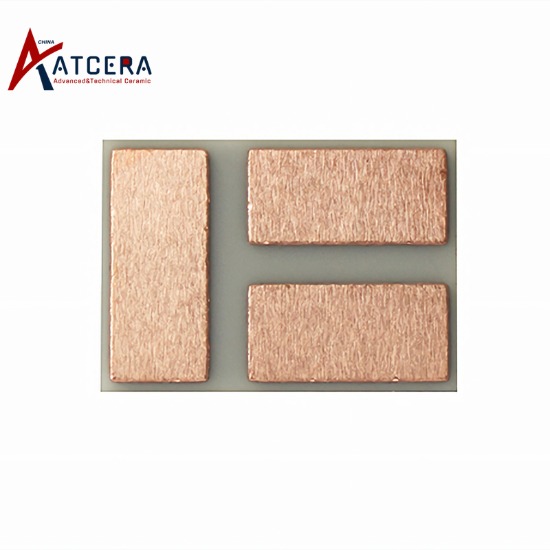
The use of Ag-Cu-Ti active filler metal includes the following four forms, which vary with the form of Ti element and the combination of filler metal:
a. Pre-coated Ti powder (or TiH, powder) paste, and then add preformed solder (usually Ag72Cu28 alloy solder);
b. A layer of Ti film is deposited on the ceramic surface with PVD(physical vapor deposition) or CVD(chemical vapor deposition) in advance, and then Ag-Cu filler metal is added.
c. Use Ag-Cu-Ti solder;
d. Use Ag-Cu-Ti solder paste.
When using silver copper titanium active filler metal to prepare AMB silicon nitride substrate, the main causes of interfacial voids are as follows:
1. Surface quality of raw materials: Scratches, pits, oxidation, organic pollution on the surface of ceramic and oxygen-free copper before welding will have a negative impact on the wetting and spreading of solder, bringing potential voids risk to the brazed interface.
2. Solder printing quality: In the process of large-area solder paste printing, it is easy to have the problem of solder paste leakage and uneven printing, and once the solder is melted, it will directly lead to the formation of holes.
3. Deactivation of active elements: the active element Ti in AgCuTi solder paste is very sensitive to oxygen, and the vacuum degree is often required to be better than 10-3Pa in the process of high-temperature brazing. If the vacuum degree cannot meet the welding requirements, Ti is oxidized and deactivated, and the solder cannot wet the ceramic surface, which will cause a large area of welding, welding leakage and other phenomena.
4. Solder paste volatile gas: In the process of brazing, the gas volatilized in the solder paste will be wrapped by the flux to form bubbles, in addition, the reaction of organic acids and metal oxides in the flux will also produce bubbles, with the reaction of the bubbles gradually larger, the discharged bubbles will leave dense pores on the surface of the solder paste, and the undischarged bubbles will also stay at the brazing interface with the process of melting and solidification of the solder. Forming a void.
5. Brazing process parameters: Ag-Cu-Ti active brazing filler metal is often above 800 ℃ to wet the surface of Si3N4, if the brazing temperature is too low or the holding time is too short, the reaction between Ti and the ceramic surface is not sufficient, resulting in the brazing filler metal can not completely wet the ceramic surface.
In summary, brazing is crucial for AMB silicon nitride substrates, with Ag-Cu-Ti alloy as the primary active filler metal due to its ability to wet ceramics at 800~950 ℃ and form strong joints. However, interfacial voids are a significant issue caused by factors like raw material quality, solder printing, active element deactivation, volatile gases, and improper brazing parameters. To achieve high-quality joints, it's essential to address these challenges through refined preparation, improved techniques, optimized conditions, and enhanced process control.