With the rapid development of microelectronics technology, the requirements for electronic packaging materials are increasingly stringent. Aluminum nitride ceramics, with its excellent thermal conductivity, excellent mechanical properties, corrosion resistance and excellent electrical properties, become the leader of large-scale integrated circuit cooling substrate and packaging materials. However, the high hardness, high brittleness and low fracture toughness of aluminum nitride ceramics are like an insurmountable gap, which greatly challenges its application in the field of ultra-precision machining. Especially in the pursuit of ultra-smooth surface with surface roughness Ra ≤ 8 nm or even RMS < 2 nm, how to effectively reduce surface defects and sub-surface damage during machining has become a key problem restricting the wide application of aluminum nitride ceramics. In this context, ELID (Electrolytic in-process Dressing) grinding process offers innovative solutions to the processing challenges of AlN substrates with its unique advantages.
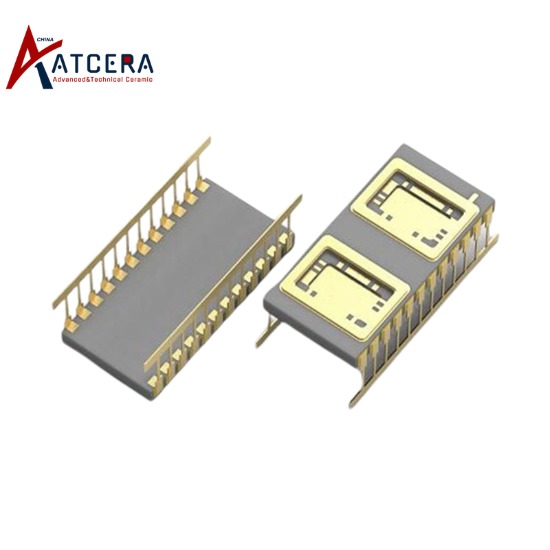
ELID grinding technology is a composite mirror processing technology that integrates traditional grinding, grinding and polishing. The core of ELID grinding technology is to realize dynamic self-sharpening during grinding through electrolytic in-situ dressing of grinding wheels, thus significantly improving grinding efficiency and processing quality. ELID grinding technology shows exceptional applicability for high-hardness brittle materials such as aluminum nitride ceramics.

Firstly, ELID grinding uses a weak electrolyte solution as the grinding fluid, which not only avoids the potential corrosion of the traditional grinding fluid on the machine tool and the workpiece, but also simplifies the processing environment and reduces the production cost. More importantly, this technology can effectively control the temperature during grinding, reducing workpiece burns, residual stresses and cracks caused by high temperatures, which is essential to protect the microstructure and properties of aluminum nitride ceramics.
Secondly, ELID grinding forms a uniform and dense oxide film on the surface of the grinding wheel through electrolysis, which not only improves the cutting ability of the grinding wheel, but also enhances the wear resistance of the grinding wheel, ensuring the stability and continuity of the grinding process. At the same time, by precisely controlling the correction current, the fine adjustment of the oxide layer thickness can be achieved, and then the grinding effect can be optimized, the surface roughness and sub-surface damage can be reduced, and the harsh requirements of aluminum nitride ceramics for ultra-smooth surfaces can be met.
In addition, ELID grinding technology also has the characteristics of simple process and flexible operation, which is easy to promote and apply in industrial production. Through continuous optimization of grinding parameters and process conditions, the processing efficiency and processing quality of aluminum nitride ceramics can be further improved to meet the growing demand for high-performance materials in the field of microelectronics packaging.
In summary, ELID grinding process, with its unique advantages, has shown great potential in solving the processing problems caused by high hardness, high brittleness and low fracture toughness of aluminum nitride ceramics. Through this technology, not only can effectively reduce the surface defects and sub-surface damage in the processing process, but also significantly improve the processing efficiency and processing quality, which lays a solid foundation for the wide application of aluminum nitride ceramics in the field of electronic packaging. In the future, with the continuous development and improvement of ELID grinding technology, it is believed that its application prospects in the field of ultra-precision machining will be broader, and contribute to the continuous progress of microelectronics technology.