With the rapid development of electronic technology, the integration and performance requirements of large-scale integrated circuits are increasing day by day. As a key supporting material, aluminum nitride ceramics have become an ideal cooling substrate and packaging material because of their excellent thermal conductivity, mechanical strength, corrosion resistance and excellent electrical properties. However, the high hardness, high brittleness and low fracture toughness of aluminum nitride ceramics pose a great challenge in the process of pursuing ultra-smooth surface quality. In particular, in the field of electronic packaging, surface roughness needs to be controlled at the nanoscale to minimize volume, reduce internal resistance and optimize heat dissipation performance. Therefore, how to use laser processing technology to achieve high quality flat processing surface of aln substrate has become a key problem to be solved in the field of material science and precision manufacturing.
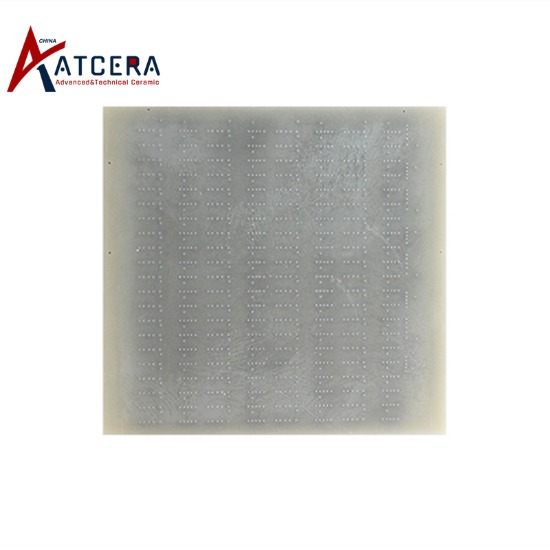
Application and challenge of laser processing technology in aluminum nitride ceramics
Laser processing technology, with its advantages of no contact, no tool wear, high precision and flexibility, has shown great potential in the processing of brittle and hard ceramic materials. In this technology, the high energy density laser beam directly acts on the surface of the material, so that the local area quickly heats up and decomposes or melts, so as to achieve the removal or modification of the material. However, for the laser processing of aluminum nitride ceramics, how to accurately control the energy distribution in the processing process, reduce the heat affected zone, avoid cracks and sub-surface damage, and ensure the high smoothness of the machined surface has become the difficulty of technical breakthrough.
Strategies for achieving high quality flatness of machined surfaces
Optimize laser parameters: By adjusting laser power, pulse width, scanning speed and spot size and other parameters, accurately control the thermal effect of laser and material interaction, reduce thermal stress concentration and avoid cracks. The research shows that the use of ultra-short pulse laser (such as femtosecond laser) can effectively reduce the heat affected zone and improve the machining accuracy.
Introduction of auxiliary gas: Inert gas (such as argon) is introduced as a protective gas during laser processing to reduce the surface oxidation of the material, while the impact effect of the gas is used to help remove melt and debris, and improve the surface finish.
Composite processing technology: Combining laser processing with other precision processing technologies (such as chemical mechanical polishing), laser roughing is performed first to remove most of the material, and then chemical mechanical polishing is used to further refine the surface to achieve the processing goal of nanoscale roughness.
Real-time monitoring and feedback control: The advanced online monitoring system is used to detect the temperature distribution, surface topography and stress state during the processing in real time, and dynamically adjust the processing parameters through the feedback control mechanism to ensure the stability of the processing quality.
conclusion
As a high performance electronic packaging material, aluminum nitride ceramics are very important to improve the overall performance of integrated circuits by obtaining high quality flat machined surfaces. With its unique advantages, laser processing technology has shown broad application prospects in the precision machining of aluminum nitride ceramics. However, in order to achieve the machining goals of nanoscale surface roughness and low damage, further research and innovation are needed in laser parameter optimization, auxiliary process introduction, composite machining strategy and machining process control. In the future, with the continuous progress and improvement of laser processing technology, we believe that we can provide more reliable and efficient solutions for the application of aluminum nitride ceramics in the field of high-end electronic packaging.