In exploring silicon nitride (Si3N4) substrate materials as core to a high-performance thermal management solution, our understanding of their heat transfer mechanisms is critical. The main heat transfer mechanism of silicon nitride is known to rely on lattice vibration, a process that transfers heat through quantized hot charge carriers called phonons.
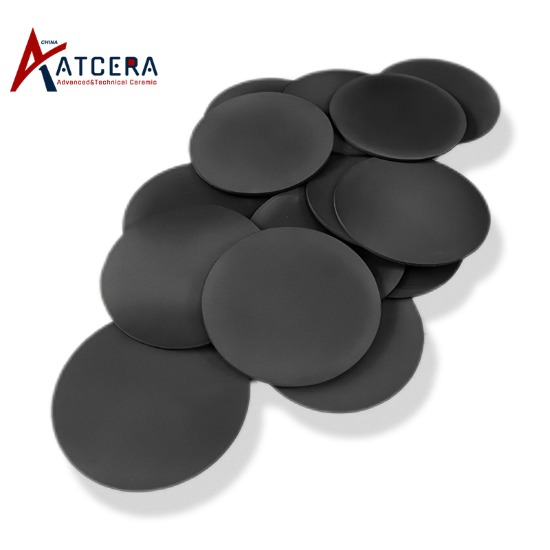
The propagation of phonons in the lattice is not a simple linear motion, but is affected by the complex coupling between the lattice, resulting in frequent collisions between phonons, which significantly reduces the mean free path of phonons, that is, the mean distance that phonons can travel freely between two collisions. This mechanism directly affects the thermal conductivity of silicon nitride materials.
Furthermore, various defects, impurities and grain interfaces in Si3N4 crystals become the main sources of phonon scattering. These scattering events also lead to a decrease in the mean free path of phonons, which in turn reduces the overall thermal conductivity of the material. In particular, lattice oxygen, as one of the main defects affecting the thermal conductivity of silicon nitride ceramics, significantly hinders the smooth propagation of phonons and reduces the thermal conductivity efficiency of the material.
To overcome this challenge and improve the thermal conductivity of the silicon nitride substrate, we started at the source and focused on reducing the oxygen content in the lattice. Specific strategies include:
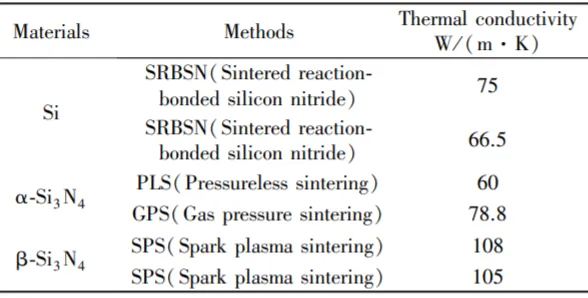
Optimize raw material powder
Choosing Si powder with low oxygen content as starting material is the key. The oxygen impurity content in the initial raw material is reduced through a rigorous raw material screening and pretreatment process. Subsequently, a two-step nitrided sintering process is used, in which Si powder is first heated in a nitrogen atmosphere to close to its melting point (1414℃), so that it reacts with nitrogen to form porous Si3N4 sintered body. This process ensures adequate nitriding of Si while controlling the oxygen content in the newly generated silicon nitride. Then, porous Si3N4 was further sintered at high temperature to promote grain growth and pore closure, and finally the Si3N4 ceramic substrate with high density, low oxygen content and high thermal conductivity was formed.
Direct sintering of high purity α-Si3N4 powder
Another way is to use high purity α-Si3N4 powder with very low oxygen content for sintering. This method avoids the conversion process from Si to Si3N4 and directly uses α-Si3N4 powders with high purity and specific crystal structure for sintering, reducing the possibility of oxygen impurity introduction. By precisely controlling sintering parameters such as temperature, atmosphere and pressure, silicon nitride substrates with high density, few defects and excellent thermal conductivity can be obtained.
Sintering application of β-Si3N4
Although β-Si3N4 may differ from α-Si3N4 in some physical properties, its low oxygen content and high purity are also suitable for the preparation of high-performance silicon nitride substrates. The use of β-Si3N4 powder for sintering can also prepare high thermal conductivity silicon nitride materials, especially in specific application scenarios, some characteristics of β-Si3N4 may be more advantageous.
In summary, the Silicon nitride (Si3N4) substrate material is a key component of a high-performance thermal management solution, and the optimization of its thermal conductivity is crucial to improve the overall thermal management efficiency. By deeply understanding the heat transfer mechanism of silicon nitride, namely lattice vibration and phonon conduction process, we realize that phonon scattering is one of the key factors affecting the thermal conductivity. In particular, oxygen defects in the lattice, acting as the main scattering source, significantly reduce the mean free path of phonons, thereby hindering the effective conduction of heat.
To overcome this challenge, we propose a variety of strategies to reduce the oxygen content in the silicon nitride substrate, thereby improving its thermal conductivity. From the optimal selection of raw material powder, to the direct sintering of high-purity α-Si3N4 powder, to the sintering application of β-Si3N4, each method aims to reduce the introduction of oxygen impurities at the source and achieve high density and low defect status of the material through fine process control.
Future research will further focus on exploring more efficient silicon nitride preparation processes and further understanding the mechanism by which different crystal structures and microstructure affect the thermal conductivity of silicon nitride. Through these efforts, we are expected to develop silicon nitride substrate materials with higher thermal conductivity and lower thermal resistance, providing strong support for high-performance thermal management in electronic packaging, aerospace, energy conversion and other fields.