In practical applications, in addition to high thermal conductivity and high electrical insulation properties, aluminum nitride substrates are also required to have high bending strength in many fields. At present, the three-point bending strength of aluminum nitride in circulation on the market is usually 400~500MPa, which seriously limits the promotion and application of aluminum nitride ceramic substrates, especially in the field of IGBT power devices with high reliability requirements. Due to the complex production process and high production cost of AlN materials, most of the domestic AlN materials are still unable to meet the application requirements of high thermal conductivity and high strength.
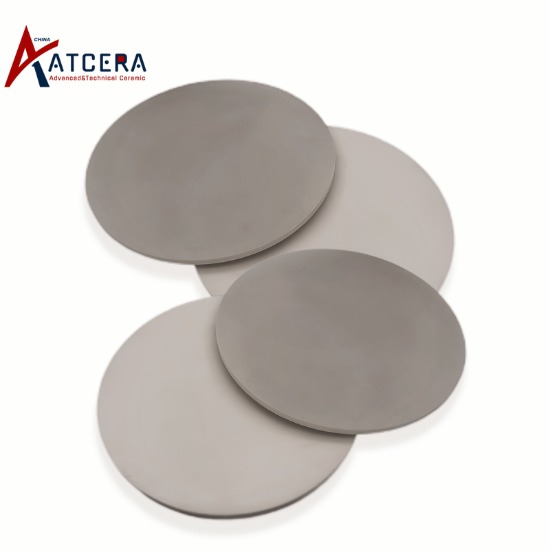
In the preparation of aluminum nitride ceramic substrate, the selection of sintering methods and sintering additives is often twice the result with half the effort, and the introduction of sintering additives is a common method for sintering aluminum nitride ceramics at present. On the one hand, the formation of low temperature eutectic phase, the realization of liquid phase sintering, promote the compact body; On the other hand, the oxygen impurity in aluminum nitride is removed, the lattice is improved, and the thermal conductivity is increased. At present, the sintering additives used in sintering AlN ceramics mainly include Y2O3, CaO, Yb2O3, Sm2O3, Li2O3, B2O3, CaF2, YF3, CaC2, etc., or their mixtures.
In the sintered aluminum nitride ceramic formula system, when Y2O3 is higher than 3.5wt%, the content of Y-Al-O increases significantly and aggregates in the sintering process. Due to the low thermal conductivity of Y3Al5O12 (about 9 W/ (m·K)), the thermal conductivity of aluminum nitride ceramic products after sintering is seriously affected. When the content of CaF2 and Li2O is higher than 1.33wt%, due to the volatilization of fluoride and Li-containing compounds, the porosity of the sintered aluminum nitride ceramic body is increased during the sintering process, and the density of the ceramic is reduced, resulting in a sharp decline in the bending strength of aluminum nitride ceramic products after sintering. When each additive is less than the minimum value, the effect of enhancing mechanical properties cannot be played or the effect is very small.
In summary, aluminum nitride ceramic substrate in practical applications face the comprehensive requirements of high thermal conductivity, high electrical insulation properties and high bending strength, but the flexural strength of the products in circulation on the market is generally low, limiting its wide application in the field of high reliability such as IGBT power devices. At the same time, the domestic AlN material is difficult to meet the application needs of high thermal conductivity and high strength due to the complex production process and high production cost. Therefore, in the preparation of aluminum nitride ceramic substrate, it is very important to select the appropriate sintering method and sintering additives, not only to form a low temperature eutectic phase to promote the compact body, but also to remove oxygen impurities to improve the thermal conductivity. However, the selection and dosage of sintering additives need to be strictly controlled to avoid negative effects on thermal conductivity and bending strength. In the future, in order to improve the performance of aluminum nitride ceramic substrates, it is still necessary to further optimize the sintering process and formulation system to meet the needs of higher levels of application.