In the field of high-tech materials, aluminum nitride (AlN) ceramics, with its excellent thermal conductivity, excellent electrical insulation properties and excellent mechanical strength, have become the core material in key fields such as electronic packaging, power electronics and microwave communication equipment. However, the preparation of aluminum nitride substrate is a complex process, in which the sintering process and the selection of sintering additives have important effects on the properties of the final product. In this paper, starting from the preparation process of aln ceramic substrate, the selection of sintering additives and their influence on the performance of the substrate will be discussed in detail, and combined with frontier research, how to improve the comprehensive performance of aluminum nitride substrate by optimizing the sintering additives and sintering process will be analyzed.
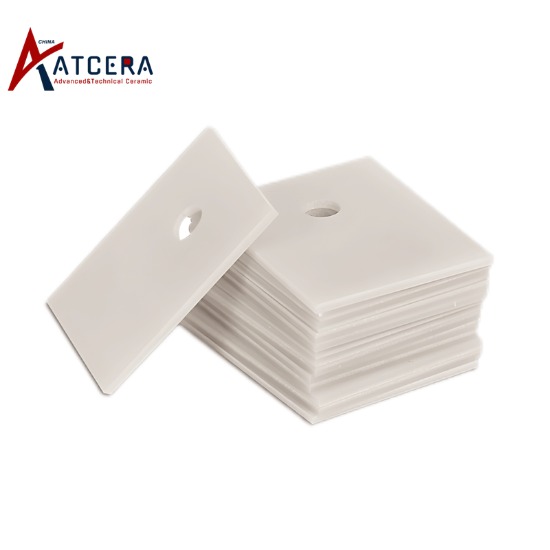
Preparation Technology of Aluminum Nitride Substrate
The preparation of aluminum nitride substrate mainly includes raw material preparation, mixing, molding, sintering and other key steps.
1. Raw material preparation
Raw material preparation is the first step in the preparation of aluminum nitride ceramic substrate, which mainly includes the selection and ratio of aluminum nitride powder, alumina powder and additives. As the main material, aluminum nitride powder is required to have the characteristics of high purity, small particle size, large specific surface area, low carbon content and low oxygen content. Alumina powder is usually used as part of the sintering aid to form a low melting point composite oxide during the sintering process to promote the densification of aluminum nitride ceramics. Additives are used to regulate the molding properties, sintering properties and mechanical properties of the material.
2. Mix and form
In the mixing process, it is necessary to mix aluminum nitride powder, alumina powder and additives according to a certain ratio to ensure the uniformity and stability of subsequent molding. Mixing can be done by dry or wet method. Molding is usually by pressing molding, injection molding or die molding, etc., the mixed raw materials are made into billets with a certain shape and size.
3. Sintering
Sintering is the last process and the most critical step in the preparation of aluminum nitride ceramic substrate. Under the condition of high temperature, the particles in the billet are combined by sintering to form a dense ceramic substrate. In the sintering process, temperature, atmosphere and time need to be controlled to ensure the forming quality and performance of the ceramic substrate. The commonly used sintering processes include hot pressing sintering, non-pressing sintering, microwave sintering, discharge plasma sintering and self-propagating sintering.
The Selection of Sintering Additives and Its Influence on The Properties of Substrate
Sintering additives play an important role in the preparation of aluminum nitride ceramic substrates. They react with the alumina composition on the surface of the aluminum nitride particle to form a composite oxide with a low melting point, resulting in a liquid phase in the sintered body. These liquid phases surround the aluminum nitride particles, and the particle rearrangement and internal pore discharge occur under the action of capillary force, and finally the compact sintering of aluminum nitride ceramics is realized.
1. Commonly used sintering additives
The commonly used sintering auxiliaries for aluminum nitride ceramic substrates include CaO, Li2O, B2O3, Y2O3, CaF2, CaC2 and CeO2. These materials play a dual role in the sintering process: first, they combine with aluminum oxide on the surface of aluminum nitride particles to form liquid aluminate, accelerating mass transfer and promoting sintering; Secondly, they can react with oxygen to reduce the lattice oxygen content and increase the thermal conductivity of aluminum nitride ceramics.
2. Principle of selection of sintering additives
When selecting sintering additives, it is necessary to consider their influence on the properties of aluminum nitride ceramic substrate. On the one hand, the sintering additives should promote the densification of aluminum nitride ceramics, improve the thermal conductivity and mechanical strength; On the other hand, sintering additives should avoid the introduction of excessive impurities, so as not to affect the electrical insulation properties and chemical stability of aluminum nitride ceramics. Therefore, when selecting sintering additives, a lot of experiments and optimization are needed to determine the best sintering additives formula.
3. Influence of sintering additives on substrate performance
The selection and content of sintering additives have significant influence on the performance of aluminum nitride ceramic substrate. For example, Y2O3, as one of the commonly used sintering additives, can significantly improve the thermal conductivity and bending strength of aluminum nitride ceramics when the content is moderate. However, when the content of Y2O3 is too high, Y-Al-O phase will be formed, resulting in a significant decrease in thermal conductivity. Therefore, when preparing aluminum nitride ceramic substrate, it is necessary to precisely control the content of sintering additives to obtain the best performance.
Improved Performance of AlN Substrate
In order to meet the high requirements for the performance of aluminum nitride ceramic substrates in different application fields, researchers are constantly exploring new sintering additives, optimizing sintering processes and developing new preparation technologies.
1. Development of new sintering additives
In order to further improve the performance of aluminum nitride ceramic substrates, researchers are actively developing new sintering additives. For example, by introducing rare earth elements or transition metal elements, the lattice structure of aluminum nitride ceramics can be optimized to improve thermal conductivity and mechanical properties. In addition, a variety of properties can be achieved through the use of composite sintering additives.
2. Optimization of sintering process
The optimization of sintering process is the key to improve the performance of aluminum nitride ceramic substrate. By adjusting sintering temperature, holding time and atmosphere, the microstructure of aluminum nitride ceramics can be accurately controlled. For example, rapid sintering methods such as microwave sintering or discharge plasma sintering can significantly shorten the sintering time and improve the production efficiency. At the same time, the microstructure and properties of Al nitride ceramics can be further optimized by precisely controlling the oxygen content and temperature gradient in the sintering atmosphere.
3. Innovation of preparation technology
With the continuous development of preparation technology, researchers are constantly exploring new preparation methods to improve the performance of aluminum nitride ceramic substrates. For example, the precise preparation of aluminum nitride ceramic substrate can be achieved by using advanced molding technologies such as casting molding and injection molding. In addition, the welding performance, stability and corrosion resistance of aluminum nitride ceramic substrate can be further improved by electroless copper plating, ceramic substrate encapsulation and other post-treatment processes.
Conclusion
In summary, the preparation of aluminum nitride ceramic substrate and the selection of sintering additives have important effects on its properties. The comprehensive properties of aluminum nitride ceramic substrate can be significantly improved by optimizing the sintering auxiliary formula, improving the sintering process and developing new preparation technology. In the future, with the continuous development of material science and preparation technology, the application field of aluminum nitride ceramic substrate will be further expanded, providing strong support for the development of electronic packaging, power electronic devices and microwave communication equipment. At the same time, we also need to pay close attention to the development trend of new technologies and new materials, constantly expand the research horizon, and promote the continuous progress and innovation of aluminum nitride ceramic substrate technology.