Silicon nitride ceramics, with its light specific gravity, high strength, wear resistance, excellent electrical insulation and self-lubrication properties, stand out in the field of ceramic bearings, especially under extreme working conditions such as high speed, high temperature, low torque and lean oil lubrication, silicon nitride ball as a rolling body ceramic bearings show excellent application potential. However, the strong covalent bond properties of silicon nitride make it difficult to densify through solid phase sintering, which brings challenges to the preparation of silicon nitride ceramics. In this paper, the liquid phase sintering process of silicon nitride ceramics, including atmospheric sintering, hot pressing sintering and pressure sintering, and the influence of these processes on the microstructure and mechanical properties of silicon nitride ceramics are discussed.
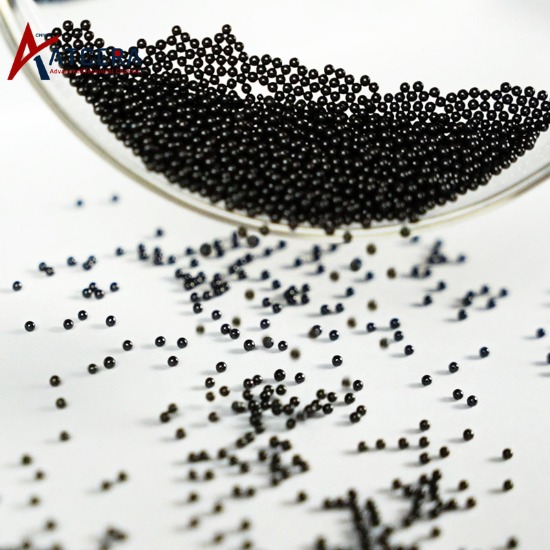
Silicon nitride ceramic is the first choice of ceramic bearing roller with its excellent properties such as light weight, high strength, abrasion resistance, electrical insulation and self-lubrication. Ceramic bearings with silicon nitride ceramic balls as rolling bodies are particularly suitable for use under working conditions such as high speed, high temperature, low torque and lean oil lubrication, such as high-speed motorized spindle bearings for precision machine tools, wind power bearings and aerospace bearings.
Silicon nitride is a strong covalent bond compound with low self-diffusion coefficient and insufficient sintering driving force, so it is difficult to achieve densification by simple solid phase sintering. Therefore, a certain amount of sintering additives need to be added to complete the densification process by liquid phase sintering. The principle of liquid phase sintering of silicon nitride ceramics is that sintering additives react with SiO2 on the surface of silicon nitride powder to form a liquid phase, and under the action of the liquid phase, it reaches densification through the process of particle rearrangement, solution-precipitation and grain growth.
The commonly used liquid phase sintering methods of silicon nitride ceramics include atmospheric pressure sintering, hot press sintering and air pressure sintering.
Silicon nitride begins to decompose after 1700℃, in order to inhibit the decomposition of silicon nitride, atmospheric pressure sintering is usually carried out by buried powder, but the effect of buried powder is limited, so that the temperature of atmospheric pressure sintering can not exceed 1750℃, and a large number of sintering additives need to be added to promote densification, which seriously affects the performance of the product.
Hot press sintering is to achieve densification under the double action of liquid phase and mechanical pressure, the sintering temperature is low, and the product performance is excellent, but due to the limitation of the graphite mold, it can only be used to produce products with simple shapes, and the production capacity is low.
Pressure sintering (GPS) relies on high pressure nitrogen (1 ~ 10 MPa) to inhibit the decomposition of silicon nitride, can increase the sintering temperature of silicon nitride ceramics to more than 1900 ℃, solve the contradiction between densification and high temperature decomposition of silicon nitride ceramics sintering process, can reduce the amount of sintering additives, improve the performance of products, suitable for mass production.
At present, there are a lot of literature reports on the effect of pneumatic sintering process on the microstructure and mechanical properties of silicon nitride ceramics.
For example, Zhou Changling et al. used β-Si3N4 powder as raw material and yttrium aluminum garnet (YAG) as sintering agent to produce silicon nitride ceramics by pressure sintering process, and found that the densification degree and mechanical properties of silicon nitride ceramics first increased and then decreased with the increase of sintering temperature.
Mitomo et al., using α-Si3N4 powder and β-Si3N4 powder as raw materials and MgO-Y2O3 as sintering agent, studied the differences in the microstructure of silicon nitride ceramics sintered by pressure of different raw materials, and found that under the same conditions, the microstructure of silicon nitride ceramics prepared with α-Si3N4 powder as raw materials showed a bimodal state and coarse β-Si3N4 grains The microstructure of silicon nitride ceramics prepared with β-Si3N4 powder was uniform and showed unimodal state.
In summary, the preparation process of silicon nitride ceramics, especially the liquid phase sintering technology, has a crucial effect on its microstructure and mechanical properties. By comparing the advantages and disadvantages of different methods such as atmospheric sintering, hot pressing sintering and pneumatic sintering, we can find that pneumatic sintering has outstanding performance in increasing sintering temperature, inhibiting the decomposition of silicon nitride, reducing the amount of sintering additives and improving the performance of products, and is suitable for mass production of high-performance silicon nitride ceramics. At the same time, the selection of different raw materials and sintering additives also has a significant effect on the microstructure and mechanical properties of silicon nitride ceramics. In the future, with the deepening of research and continuous progress of technology, the preparation process of silicon nitride ceramics will be more perfect, and its application in precision machine tools, wind power, aerospace and other fields will be more extensive.