Introduction to Alumina Ceramics
Alumina ceramics, with their exceptional properties such as high hardness, high-temperature resistance, oxidation resistance, corrosion resistance, high electrical insulation, and low dielectric loss, have become the most widely produced and applied advanced ceramic material. They are extensively used in various industries including metallurgy, chemicals, electronics, and biomedicine.
These ceramics are often classified based on the Al2O3 content in their composition. For instance, "75 porcelain" contains approximately 75% Al2O3. Due to its lower sintering temperature, the cost of production for 75 porcelain is relatively low compared to other alumina ceramics. However, its average performance has led to its phased-out status in most applications.
"85 porcelain," with an Al2O3 content of around 85%, often includes additives like talc powder to enhance the mechanical strength and electrical properties of the ceramic. This type is commonly used in the manufacture of electric vacuum devices.
"95 porcelain," containing about 95% Al2O3, is primarily employed in corrosion-resistant and wear-resistant components.
"99 porcelain," with a 99% Al2O3 content, offers excellent high-temperature resistance, wear resistance, and corrosion resistance. It finds applications in special refractory and wear-resistant devices such as ceramic bearings, furnace tubes, and crucibles.
Ceramics with an Al2O3 content exceeding 99.9% are known as "high-purity alumina ceramics." These ceramics, with a sintering temperature exceeding 1650℃, possess transmittance properties, making them suitable for devices like sodium lamp tubes. Additionally, they are used in electronic components such as integrated circuit substrates and high-frequency insulation materials.
Sintering Techniques for Alumina Ceramics
2.1 Pressureless Sintering
Pressureless sintering involves the process of sintering the green body under atmospheric conditions without any external pressure. The material begins to sinter without external pressure, typically at temperatures ranging from 0.5 to 0.8 of the material's melting point. Solid-phase sintering at these temperatures allows for sufficient atomic diffusion. This method, known for its simplicity and cost-effectiveness, is widely used in industrial production. It can sinter materials of various shapes and sizes, making it a popular choice for nano-ceramics. Advanced sintering techniques like rapid sintering and two-step sintering have evolved from this method.
2.1.1 Conventional Sintering
Conventional sintering involves heating the material to the maximum sintering temperature at a traditional one-step rate, holding it for a period, and then cooling to room temperature. This method is considered effective only for easily sinterable materials with excellent powder properties, high green density, and uniform structure. Studies have examined the influence of molding pressure and powder grain size on ceramic sintering. Using conventional pressureless sintering, Li et al. achieved an alumina nano-ceramic with a grain size of 90nm and a density of about 90% by heating at a rate of 10ºC/min to 1450ºС for 1 hour. The study found a positive correlation between green density, ceramic density, and molding pressure, highlighting the importance of achieving a uniform and high-density green body for pressureless conventional sintering of nano-ceramics.
2.1.2 Two-Step Sintering
There are two primary forms of this method, as illustrated in Figures 1a and 1b, proposed by Chu et al. and Chen et al., respectively. The former involves initial low-temperature sintering, by high-temperature sintering and cooling. This method provides better control over the ceramic's microstructure and improves its properties, but often results in larger ceramic grain sizes. The latter technique involves heating the green body to a temperature (t1), where partial densification occurs, with a relative density between 75% and 90%. Some pores remain in a metastable state. The temperature is then lowered to a relatively lower t2 and held for an extended period. This allows for final densification through diffusion at lower temperatures while inhibiting grain growth, enhancing the mechanical properties of the sintered ceramic. The essence of this method lies in exploiting the kinetic differences between grain boundary migration and diffusion to suppress grain boundary migration during the later stages of sintering. Compared to rapid sintering, which focuses on suppressing grain coarsening during the early sintering stages, this method proves more effective for preparing nano-ceramics.
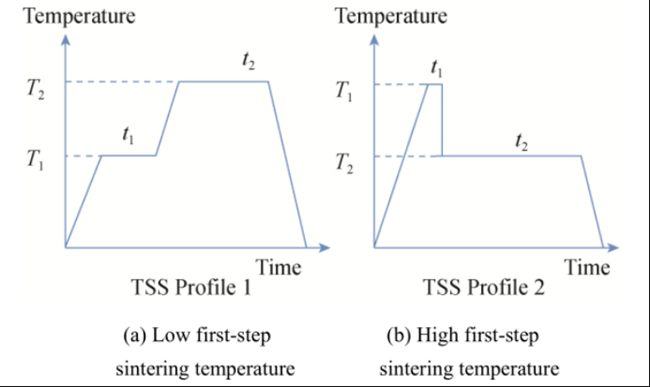
Figure 1
2.2 Hot Pressing Sintering
Hot pressing sintering involves heating the powder while applying uniaxial stress at high temperatures. This allows the sintered body to densify primarily through material migration under external pressure. Hot pressing can be classified as vacuum, atmosphere, or continuous, and its sintering temperature is much lower than that of atmospheric sintering. For alumina, conventional sintering at atmospheric pressure requires heating to 1800℃, whereas hot pressing (at 20MPa) needs only about 1500℃. Additionally, sintering at lower temperatures inhibits grain growth, resulting in a dense, fine-grained sintered body with low porosity and high strength. Kear et al. produced nano-alumina ceramics with a grain size of less than 50nm and a density of 98% by sintering Al2O3 powder at 800℃ for 15 minutes under 8GPa pressure.
Hot pressing involves either pre-forming or directly loading the powder into a mold, making the process simple. The sintered products have a high density, theoretically reaching 99%. However, this method has limitations, such as difficulty in producing complex shapes, small production scale, and high costs.
2.3 Hot Isostatic Pressing Sintering
Essentially, hot isostatic pressing is a variation of hot pressing. It involves sintering the green body in a gaseous environment at high temperatures, subjecting it to pressure from all directions. This further enhances the density of the ceramic material produced. Hot isostatic pressing offers several advantages, including reduced sintering time, lower sintering temperatures, uniform microstructure, and excellent performance. However, the high cost of equipment, consumption of large amounts of gas during the process, and limitations imposed by the softening temperature of the encapsulation material hinder its large-scale application.
2.4 High-Vacuum Sintering
High-vacuum sintering involves sintering in a highly vacuumed environment. Wang et al. used high-purity alumina (purity >99.99%) as the raw material, employing isostatic pressing technology, and sintered it at 1500℃ in a vacuum. The resulting high-purity alumina ceramic exhibited excellent performance, including high bending strength and a grain size of 2-3μm. Gustavo et al. employed high-vacuum sintering to produce alumina ceramics with high relative density and bending strength. Studies have shown that high-vacuum sintering for high-purity alumina ceramics not only reduces impurities at grain boundaries but also decreases the likelihood of porosity.
2.5 Microwave Sintering
Microwave sintering involves the interaction of the microwave electromagnetic field with the material medium, causing dielectric loss and resulting in simultaneous heating of both the surface and interior of the material. Lu et al.'s results indicate that microwave sintering of high-purity α-Al2O3 ceramics offers advantages over traditional sintering methods. These include lower sintering temperatures, significantly reduced sintering time, minimal change in grain size before and after sintering, and a more uniform and dense sintered body. This provides an important process for developing nano-dental ceramic materials.
The benefits of microwave sintering include rapid heating rates, enabling fast sintering and grain refinement, uniform heating of the ceramic product with a homogeneous internal temperature field, selective heating of material parts for repair or defect healing, energy efficiency (with potential savings of up to 50%), and the absence of thermal inertia for instant temperature changes. However, a detailed understanding of the electromagnetic field properties and distribution within the microwave cavity, microwave-material interactions, material transformations, and heat transfer mechanisms is still needed to optimize the process. As microwave sintering is a relatively new technology, its industrial implementation may take considerable time, making it a focus of future research.
2.6 Spark Plasma Sintering (SPS)
Spark Plasma Sintering utilizes pulse energy, discharge pulse pressure, and the instantaneous high-temperature field generated by Joule heating to heat the material to the sintering temperature. Compared to conventional sintering methods, Spark Plasma can produce high temperatures with a heating rate of up to 1000℃/min. The surface of the grains is activated by the plasma, accelerating sintering densification and resulting in high sintering efficiency.
SPS technology offers several advantages, including low sintering temperatures, short holding times, rapid heating rates, adjustable sintering pressures, and the ability to achieve multi-field coupling (electric-mechanical-thermal). In addition to common ceramics like Al2O3, SPS technology can also be used for the preparation of difficult-to-sinter materials such as ZrB2, HfB2, ZrC, and TiN.
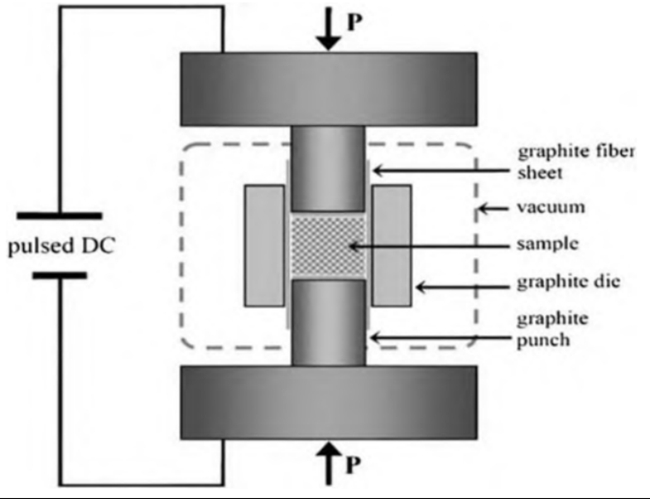
Spark Plasma Sintering Technology