Silicon carbide (SiC) as a high performance semiconductor material, because of its excellent physical and chemical properties, in power electronics, radio frequency microwave, optoelectronics and other fields show great application potential. However, the high hardness and stable lattice structure of silicon carbide pose great challenges to its polishing process. This article will focus on the reasons for the difficulty of polishing silicon carbide substrate, in order to provide reference for the research and application in related fields.
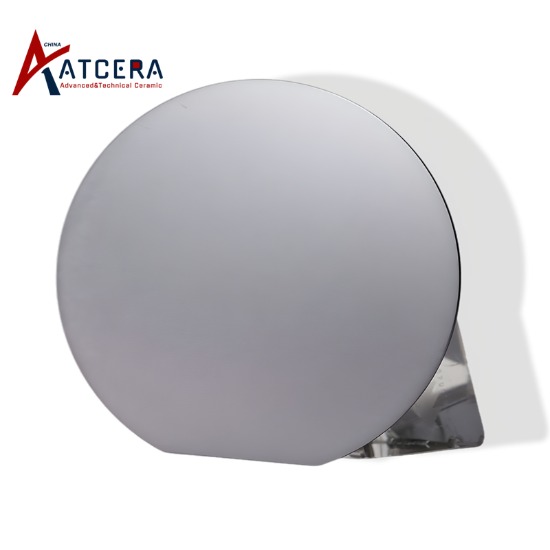
First, high hardness and brittleness caused by polishing problems
The ultra-high hardness of silicon carbide is one of its remarkable characteristics, and the Mohs hardness is up to 9.5, second only to diamond. This high hardness characteristic makes it necessary to use equally high hardness abrasives and tools in the polishing process. However, high hardness abrasives often lead to rapid wear of polishing tools during the polishing process, which not only reduces the polishing efficiency, but also may lead to a decline in polishing quality. In addition, the brittleness of silicon carbide is also a major problem in the polishing process. In the polishing process, SiC substrate is prone to cracking, forming surface damage and cracks, these defects not only affect the appearance quality of the wafer, but also may affect its electrical performance and reliability.
Second, the polishing challenge brought by the stable lattice structure
The lattice structure of SiC is composed of Si-C tetrahedrons, which has a close packed structure and high stability. This stable lattice structure makes it extremely difficult to change the surface structure by external machining means. In the polishing process, to break the covalent bond between Si-C atoms, to achieve material removal and surface quality improvement, it needs to consume a lot of heat energy and friction shear force. This not only increases the energy consumption and time cost of the polishing process, but also may cause damage to the internal structure of the chip.
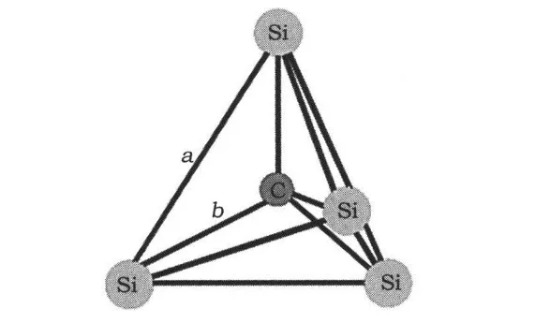
Third, the impact of stress in the polishing process
In the traditional polishing process, the workpiece and the polishing die are usually fixed by bonding glue. However, due to the inconsistent coefficient of thermal expansion between the SiC substrate and the polishing die, stress will occur at the bonding site after cooling and curing. These stresses will adversely affect the shape and finish of the wafer surface during polishing, resulting in a decline in polishing quality. In addition, the friction heat and mechanical stress generated during the polishing process can further exacerbate this effect, making the polishing process more difficult to control.
Fourth, the selection of polishing fluid and polishing pad
Polishing fluid and polishing pad are the key elements in the polishing process, and their selection directly affects the polishing effect. For silicon carbide substrates, because of its high hardness and brittleness, the traditional polishing fluid and polishing pad are often difficult to meet its polishing requirements. On the one hand, the composition of the polishing liquid, the particle size and the concentration of the abrasive need to be precisely controlled to avoid excessive damage to the chip; On the other hand, the hardness, elasticity and surface topography of the polishing pad also need to match the characteristics of the silicon carbide substrate to achieve the best polishing effect. However, special polishing fluids and polishing pads for SiC substrates are still scarce on the market, which further increases the difficulty and cost of the polishing process.
In summary, the reasons for the difficulty of polishing silicon carbide substrates mainly include its high hardness and brittleness, stable lattice structure, the influence of stress in the polishing process, and the selection of polishing fluid and polishing pad. These challenges not only affect the polishing efficiency and quality of SiC substrates, but also limit its application and development in related fields. Therefore, it is necessary to strengthen the research and innovation of silicon carbide substrate polishing technology in the future to overcome these problems and promote the wide application and development of silicon carbide materials.