At present, the production of new materials in wet chemistry is often processed by separating media such as plate frame, centrifuge, diatomite and polymer in the process of washing, classification and recovery of ultrafine powder. ATCERA inorganic ceramic membrane cross-flow filtration is an international leading process, the principle of which is to introduce the liquid to be treated into the filtration system, part of the liquid and small molecules permeate through the membrane holes to form a filter liquid; Large molecules and particles are trapped on the surface of the membrane to form a concentrated liquid. The liquid in the system flows parallel to the surface of the ceramic film, which makes it difficult for particles to form a sedimentary layer on the surface of the film and reduces the blockage of the film. Ceramic membrane pore size range from microfiltration (1.4-0.1μm) to ultrafiltration (100-5nm) to nanofiltration adjustable, acid and alkali resistance, oxidation resistance, wear resistance, high temperature resistance and easy cleaning, reflecting the revolutionary excellent advantages.
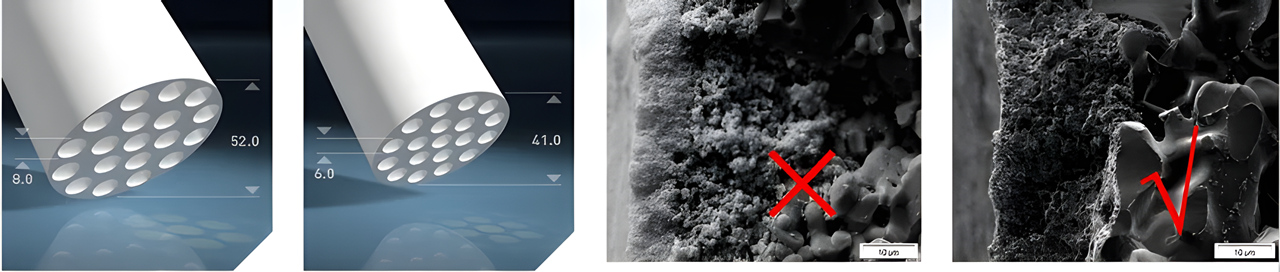
Advantages of silicon carbide ceramic membrane components
1, high precision: the fine pore structure of silicon carbide membrane tube can effectively separate fine abrasive particles, so that the produced abrasive particles have a more uniform particle size distribution;
2, corrosion resistance: chemical resistance, can deal with abrasive suspension containing strong acid, strong alkali and other corrosive chemicals, improve the service life and stability of equipment;
3, high strength: high mechanical strength, can withstand high pressure and high-speed fluid impact, suitable for processing high concentration abrasive suspension, to ensure stable filtration effect;
4, high temperature resistance: excellent thermal stability, can work in high temperature environment, is conducive to the need for high temperature treatment of abrasive production process application;
5, continuous and efficient: the traditional plate and frame filtration is usually intermittent operation, need to stop regularly to replace and clean the filter plate and filter cloth, silicon carbide ceramic membrane cross-flow filtration is usually equipped with automatic backwashing or chemical cleaning system, can automatically remove the dirt and scale on the surface of the film, maintain filtration efficiency continuous operation.
The silicon carbide ceramic film does not improve the resistance of the ceramic film by reducing the porosity of the film layer (towards the direction of no porosity, which will naturally reduce the membrane flux), but by a new production process to eliminate the weakness of the ceramic film low film resistance.
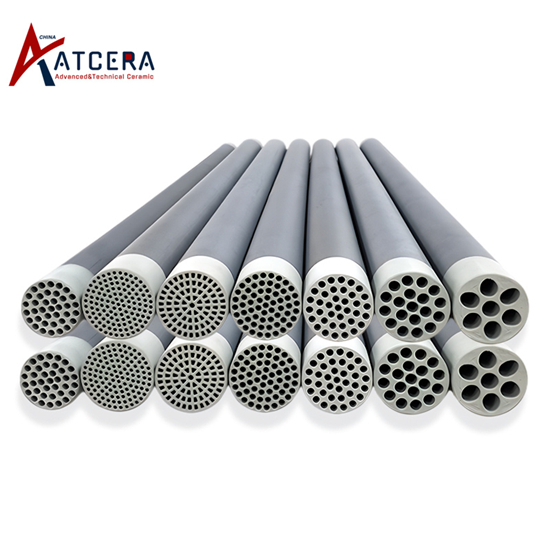
The polishing application of ceramic membrane cross-flow filtration
Based on the above advantages, silicon carbide ceramic membrane filtration can effectively separate and remove impurities and coarse particles that do not meet the size requirements in the abrasive suspension, thereby improving the purity and quality of the final product; Concentrate the abrasive particles in the abrasive suspension, reduce the subsequent drying energy consumption, and the filtrate can also be recycled and environmentally friendly; Higher levels of automation (remote monitoring by sensors) and processing efficiency (continuous production) save energy, reduce consumption, and improve system economy and reliability.