In the broad field of materials science, alumina family has become a hot spot of research and application because of its huge member system and diversified characteristics. Each member of this family has a unique preparation "code", such as alpha-alumina, which needs to be calcined in a high-temperature furnace at about 1300 ° C to show its excellent heat resistance and chemical stability; Gamma-alumina, on the other hand, has chosen a milder path, forming at relatively low temperatures of about 500 ° C and exhibiting unique physical and chemical properties. In addition, the performance of doped modified alumina can be customized by skillfully introducing iron, chromium, lanthanum and other elements. The high-purity alumina is like an artist who has the ultimate pursuit of purity, strictly excluding all external impurities.
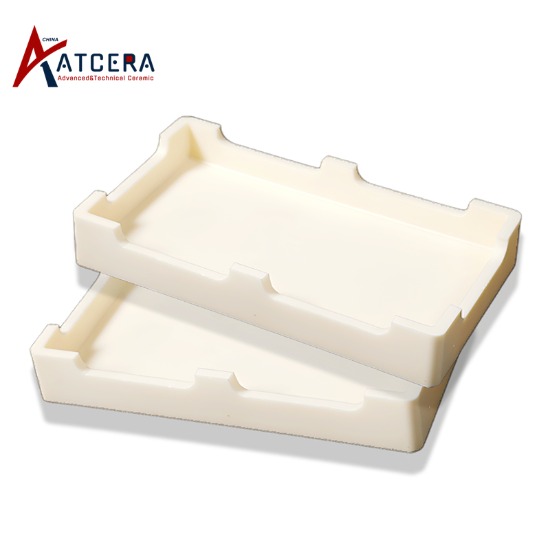
In the face of such diverse alumina production needs, the alumina tray, the vehicle in the calcination process, plays a crucial role. Traditionally, the crucible tray is made of a variety of refractory materials, its main function is to build a strong barrier for the alumina material during the calcination process, effectively prevent its direct contact with the adverse factors such as fireworks, dust and slag in the kiln, to ensure the purity and efficiency of the calcination process.
However, with the growing alumina family and the increasing complexity of preparation conditions, the traditional alumina tray has been unable to meet all the needs. To this end, a Crucible technological innovation is quietly under way. Scientists have designed customized crucible tray solutions for different alumina varieties and their specific preparation conditions. These saggers are not only more selective in material selection to ensure that they can withstand high temperatures and resist corrosion, but also optimized in structure to better adapt to the calcination characteristics of different alumina, improve production efficiency and guarantee product quality.
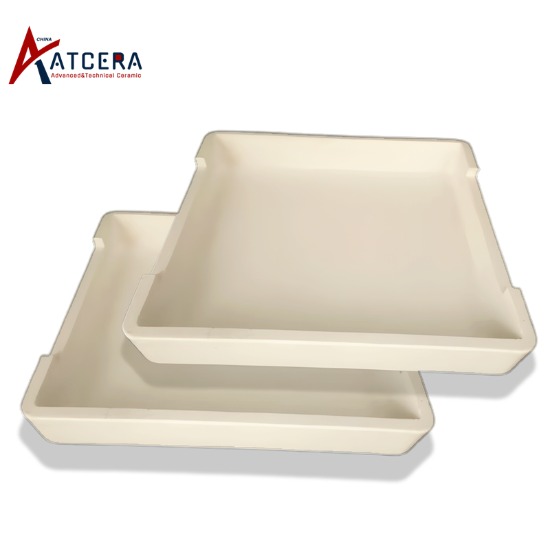
Low temperature alumina (cylindrical alumina tray)
Low temperature alumina is mainly gamma-alumina, which is generally obtained by heat treatment of its precursor pseudo-boehmite at 400 ~ 600 ° C, also known as "activated alumina". Due to the advantages of adjustable pore structure, large specific surface area, good adsorption performance, surface activity and thermal stability, gamma-alumina naturally becomes the most widely used catalyst or catalyst carrier in the chemical and petroleum industry, and can also be used in the manufacture of ceramics, refractories and abrades.
The characteristics of γ-alumina determine that it is easy to dust in the dry state, and it is easy to caking and adhesion in the wet environment. Similar to such low density and poor flow of materials and toner, etc., the cylinder tray helps overcome the difficult problem of material handling in their firing, its simple structure, easy operation, can quickly load and unload materials, improve work efficiency, and reduce labor force to a certain extent.
Abrasive and rare earth tray
The hardness and chemical activity of abrasives and rare earth materials can easily cause wear and corrosion to the vehicle, but also pollute the product due to external impurities and chemical reactions.
The abrasive and rare earth tray is mainly controlled to achieve low iron content, which improves thermal shock and corrosion resistance. High purity raw materials and special processing to achieve high surface smoothness. In the application of abrasive, rare earth, pigment calcination, its excellent wear resistance and corrosion resistance is not only conducive to the realization of no pollution to the product, but also greatly improve the service life of the crucible tray.