Because of its high hardness, high strength, excellent wear resistance and chemical stability, silicon nitride ceramics show a wide range of application prospects in ceramic bearings, cutting tools and high temperature structural materials. In this study, self-made α-Si3N4 powder was used as raw material, combined with nano-scale Y2O3 and Al2O3 as sintering additives, and silicon nitride balls were prepared by pressure sintering process with relatively low cost. The effect of sintering temperature on the densification, phase composition, microstructure and mechanical properties of ceramic balls was discussed in this paper, aiming to optimize the preparation process and improve the comprehensive properties of ceramic balls.
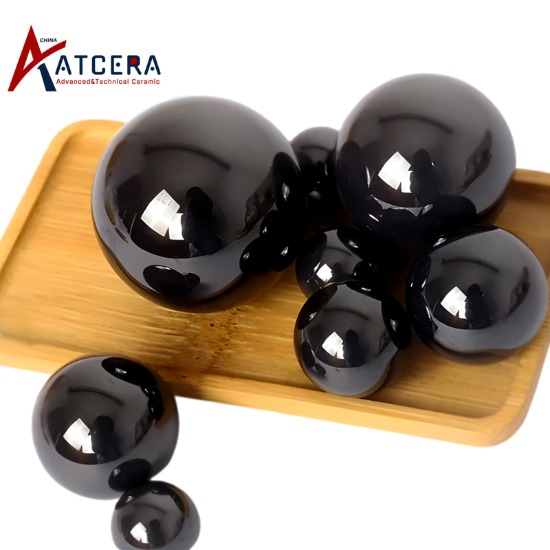
1.1 Raw materials
The raw materials used are silicon nitride powder (self-made,α-Si3N4 mass content >93%, oxygen content <2%, median particle size D50<1μm), nano-yttrium oxide (sinopyma reagent, purity >99.9%, median particle size D50<100nm), nano-alumina (sinopyma reagent, purity >99.9%, median particle size D50<100nm). Silicon nitride powder was prepared by the direct nitriding method of silicon powder, and its microscopic morphology and phase composition were shown in FIG. 1 and FIG. 2, respectively.
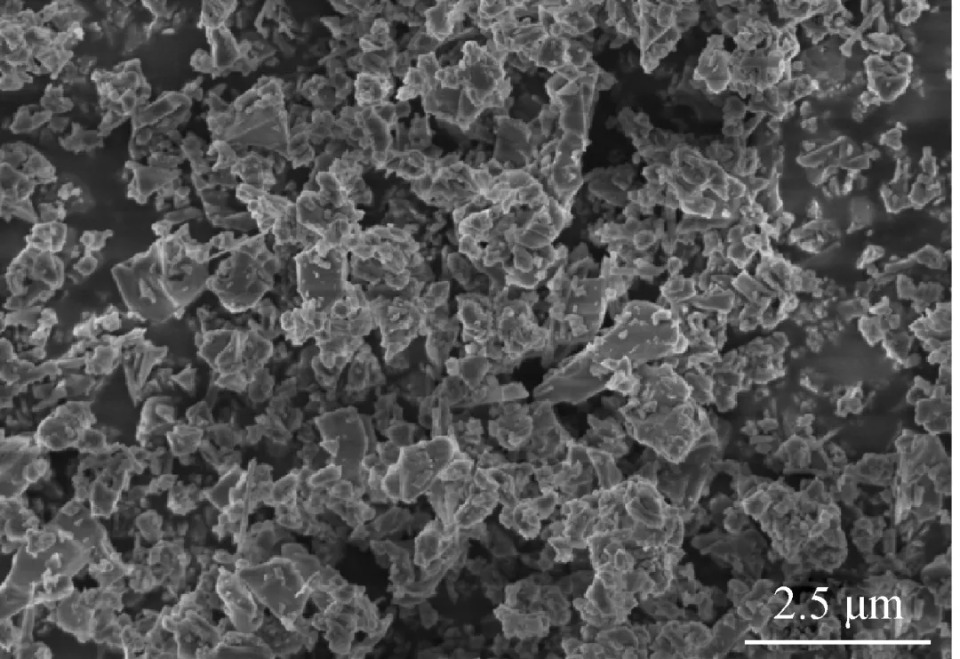
Fig.1 SEM images of silicon nitride powder
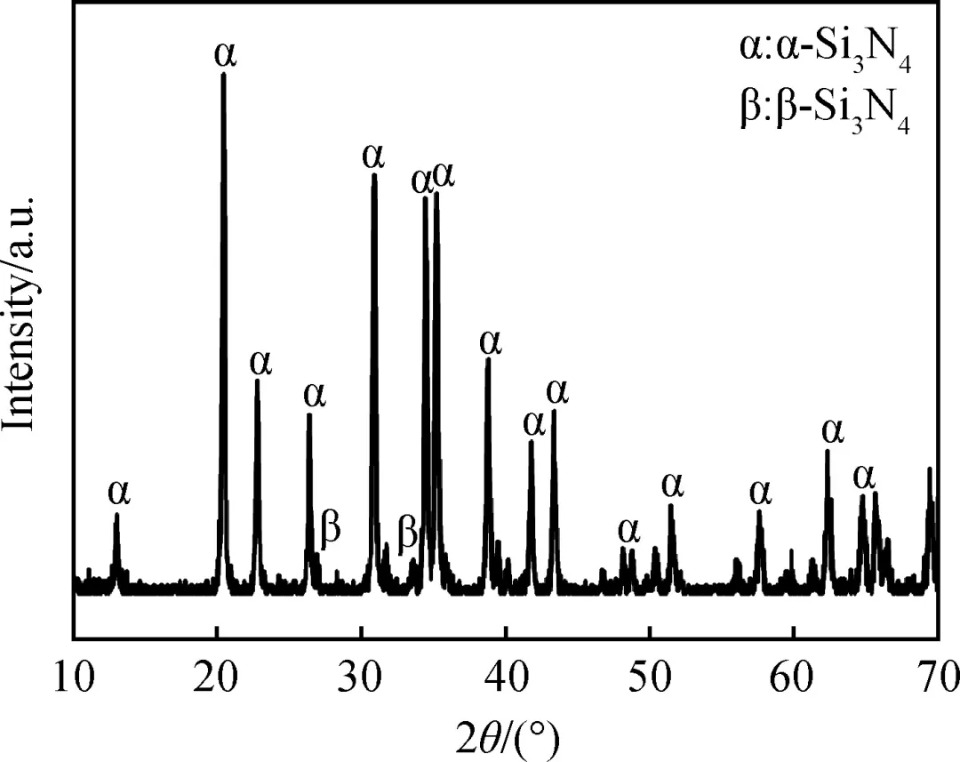
Fig.2 XRD pattern of silicon nitride powder
1.2 Test process
1.2.1 Sample preparation
According to the mass ratio of m(Si3N4) ∶m(Y2O3) ∶m(Al2O3)=92 ∶4 ∶4, the silicon nitride powder and sintering additives were added to the ball mill, and the anhydrous ethanol was used as the solvent and the silicon nitride ball was used as the grinding medium for mixing and dispersing. The evenly mixed slurry was sprayed dry and granulated, and the granulated powder was formed into 9.525mm diameter ceramic ball blank by dry pressing and cold isostatic pressing. The ceramic pellet blank was held in the air atmosphere at 500 ℃ for 1 h for the glue discharge treatment. After the glue discharge, the ceramic pellet blank was put into the atmosphere pressure sintering furnace for pressure sintering. The sintering temperature was 1720 ℃, 1750 ℃, 1780 ℃, 1800 ℃, the holding time was 3h, and the nitrogen pressure was 2MPa.
1.2.2 Analysis test
The volume density of the ceramic ball is measured by the Archimedean drainage method, and the relative density is calculated. The calculation formula is shown in equation (1). The indentation method was used to measure and calculate the Vickers hardness (load 98N) and fracture toughness (load 196N) of the ceramic ball. The calculation method of fracture toughness was referred to the method proposed by Niihara et al. The calculation formula is shown in equation (2).
According to the three-ball test method stipulated in JB/T 1255-2014 standard, the crushing load of the ceramic ball is tested and the crushing strength is calculated. The calculation formula is shown in equation (3).
The phase composition of the samples was analyzed by D8 ADVANCE X-ray diffractometer (XRD). SU8010 field emission scanning electron microscope (FE-SEM) was used to observe the microstructure of the samples, and the grain size and length-diameter ratio were measured on the random SEM photos. The number of grains in each group of samples was not less than 200.

Where :ρrd is the relative density of the ceramic ball (relative to the true density),%; ρm is the volume density of the ceramic ball,g/cm3; ρth is the theoretical density of the ceramic ball,g/cm3; ρi is the theoretical density of each phase,g/cm3; Vi is the volume fraction of each phase,%.

Where, IFR is the fracture toughness of ceramic ball,MPa·m1/2; E is the elastic modulus of the ceramic ball,GPa, where E=310 GPa; P is the load,kgf(1 kgf= 9.8N); a is the half-diagonal length of the indentation,μm; c is the length of the indentation half-tip crack,μm.

Where :σ is the crushing strength of the ceramic ball,MPa; P is the crushing load of ceramic ball,N; d is the diameter of the ceramic ball,mm.
2.1 Compaction
Figure 3 shows the relative density and changes of silicon nitride ceramic ball samples after sintering at different temperatures. It can be seen from Figure 3 that the relative density of ceramic ball samples at different sintering temperatures reaches more than 97%, and with the increase of sintering temperature, the relative density of ceramic ball first increases and then decreases.
This is because the increase in sintering temperature can reduce the viscosity of the liquid phase, promote the migration of substances and the exclusion of pores, and accelerate the growth of grains, but the sintering temperature is too high will lead to the abnormal growth of grains, aggravate the decomposition of silicon nitride and the volatilization of the liquid phase, so that the number of micropores inside the sintered body increases. Among them, the relative density of ceramic ball samples sintered at 1780 ℃ is the highest, which is 99%.
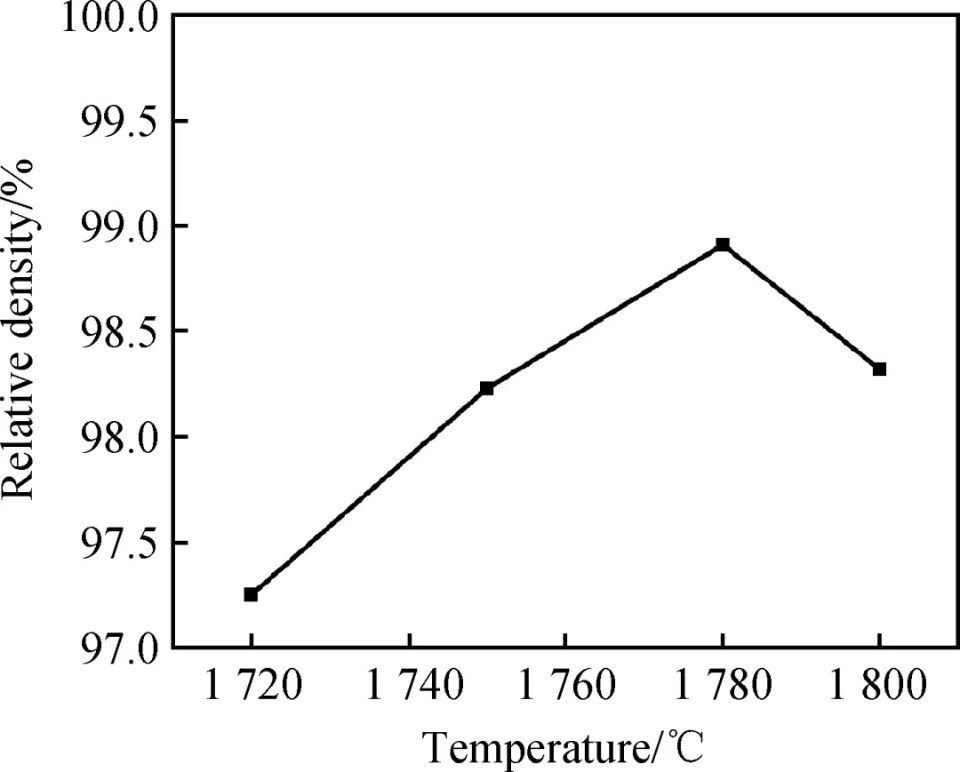
Fig.3 Effect of sintering temperatures on relative density ofceramic ball samples
2.2 Phase analysis
Figure 4 shows the XRD spectra of ceramic ball samples at different sintering temperatures. As can be seen from Figure 4, the phase composition of ceramic ball samples at different sintering temperatures is the same, consisting of β-Si3N4, Si2N2O and Y4Al2O9(YAM), and no α-Si3N4 diffraction peak is found, indicating that in 1720 At ℃ and higher temperatures,α-Si3N4 has been transformed into β-Si3N4, and with the increase of sintering temperature, the diffraction peak intensity of Y4Al2O9 gradually decreases, which may be caused by the volatilization of the liquid phase at high temperature.
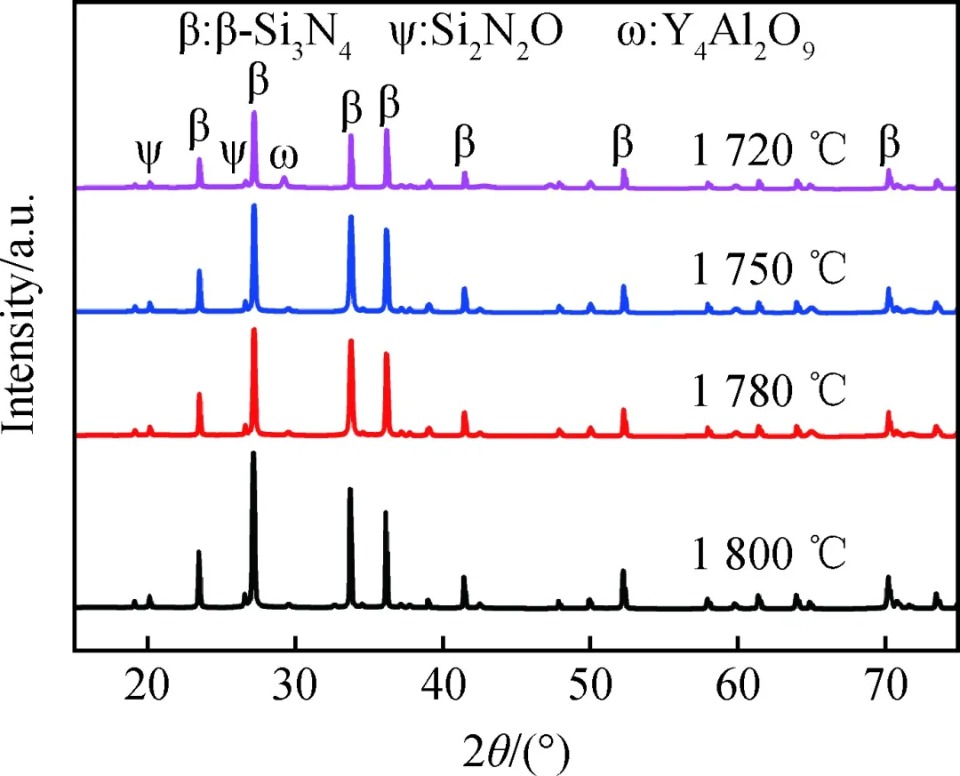
Fig.4 XRD patterns of ceramic ball samples sinteredat different sintering temperatures
2.3 Microstructure
FIG. 5 shows SEM photos of ceramic ball samples at different sintering temperatures. FIG. 6 shows the changes of grain size (i.e., diameter of long columnar grains) and length-diameter ratio of silicon nitride according to SEM photos.
It can be seen from FIG. 5 and FIG. 6 that the grain size and length-diameter ratio of silicon nitride gradually increase with the increase of sintering temperature. This is because the viscosity of the liquid phase decreases with the increase of sintering temperature, and the liquid phase with low viscosity is more conducive to mass transfer, which promotes the nucleation and growth of β-Si3N4 grains.
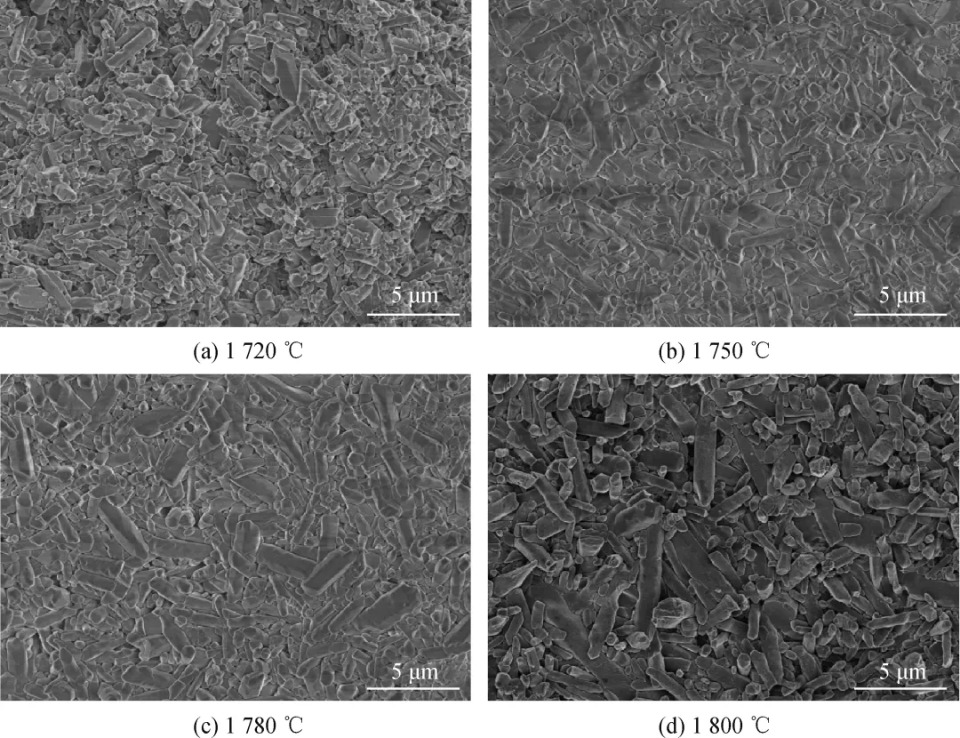
Fig.5 SEM images of ceramic ball samples sintered at different sintering temperatures
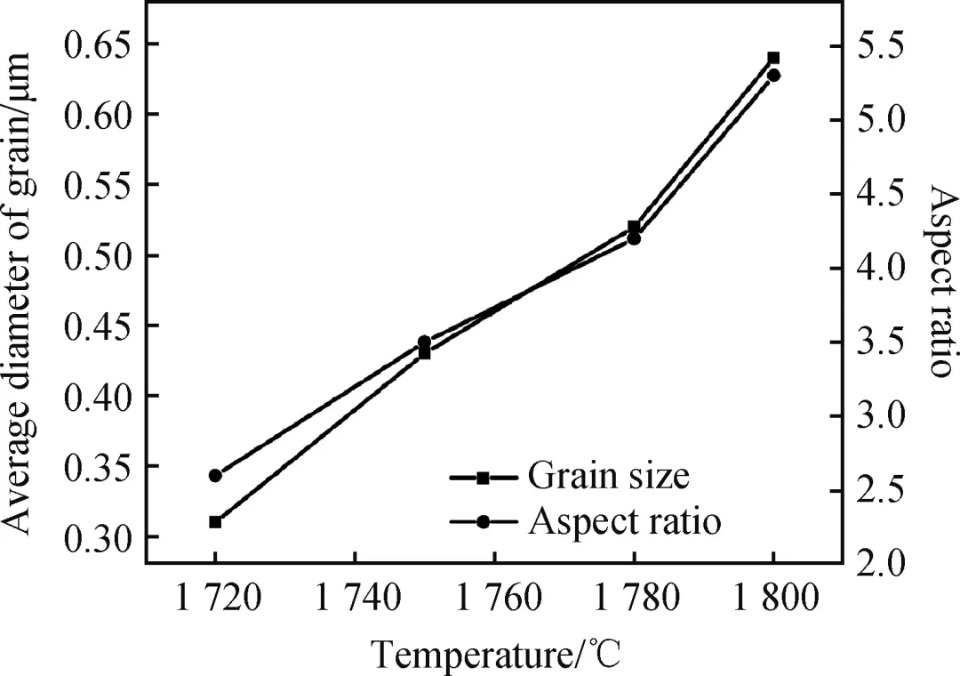
Fig.6 Effect of sintering temperature on grain size and aspectratio of ceramic ball samples
Among them, the microstructure of ceramic spheres sintered at 1720 ℃ has many pores and small grains, which are not fully developed, and the ratio of length to diameter is only 2.6. The ceramic spheres sintered at 1750 ℃ and 1780 ℃ have uniform microstructure, compact grain packing and complete development, and the ratio of length to diameter is 3.5 and 4.2, respectively. The microstructure uniformity of ceramic spheres sintered at 1 800 ℃ is poor, there are micropores, grain coarsening and abnormal growth, the ratio of length to diameter is as high as 5.3.
2.4 Mechanical properties
Figure 7 shows the changes of Vickers hardness and fracture toughness of ceramic ball samples at different sintering temperatures. As can be seen from Figure 7, with the increase of sintering temperature, the Vickers hardness of ceramic ball first increased and then decreased, and the fracture toughness continued to increase.
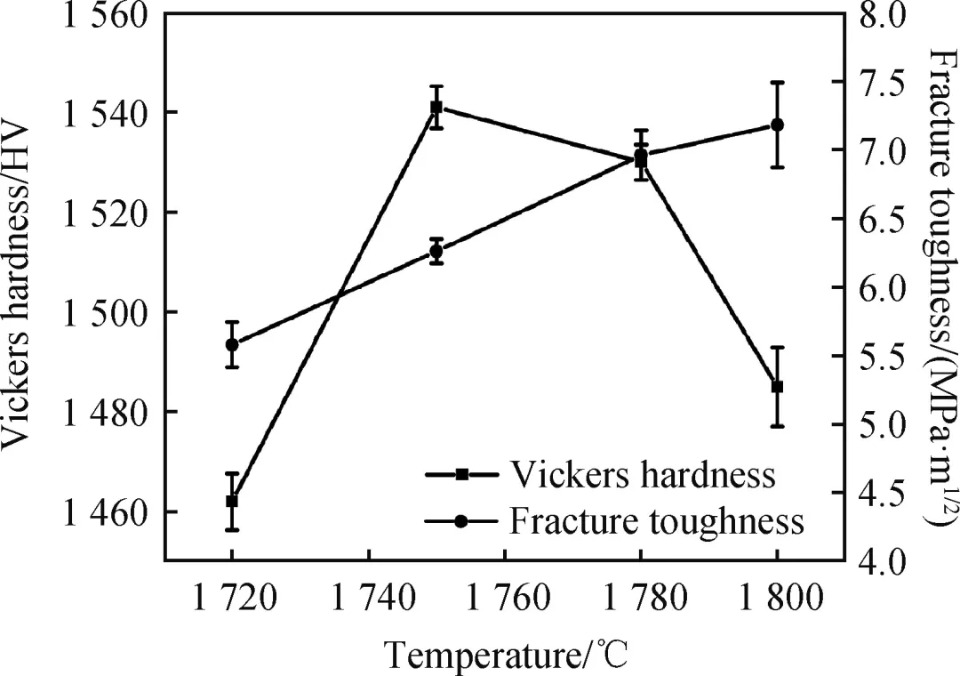
Fig.7 Effect of sintering temperature on Vickers hardness andfracture toughness of ceramic ball samples
When the sintering temperature is 1720℃, the grain size and length-diameter ratio of ceramic balls are smaller, the porosity is more, and the density is insufficient, so the Vickers hardness and fracture toughness are lower. When the sintering temperature rises to 1750℃, the grain size and length-diameter ratio of ceramic balls increase, the density increases, and the Vickers hardness and fracture toughness increase to 1540 HV and 6.3MPa·m1/2, respectively.
When the sintering temperature is 1780℃, the grain size and length-diameter ratio of ceramic balls increase further, and the fracture toughness continues to increase, reaching 7MPa·m1/2, but the Vickers hardness decreases slightly to 1530HV.
When the temperature continues to rise to 1 800 ℃, the grains of the ceramic balls grow abnormally, and there are microholes in the microstructure, causing the density to deteriorate, resulting in a sharp decline in Vickers hardness. However, the coarse long columnar grains can exert crack deflection, bridge and grain pulling out and other toughening mechanisms, which further improve the fracture toughness of the ceramic balls.
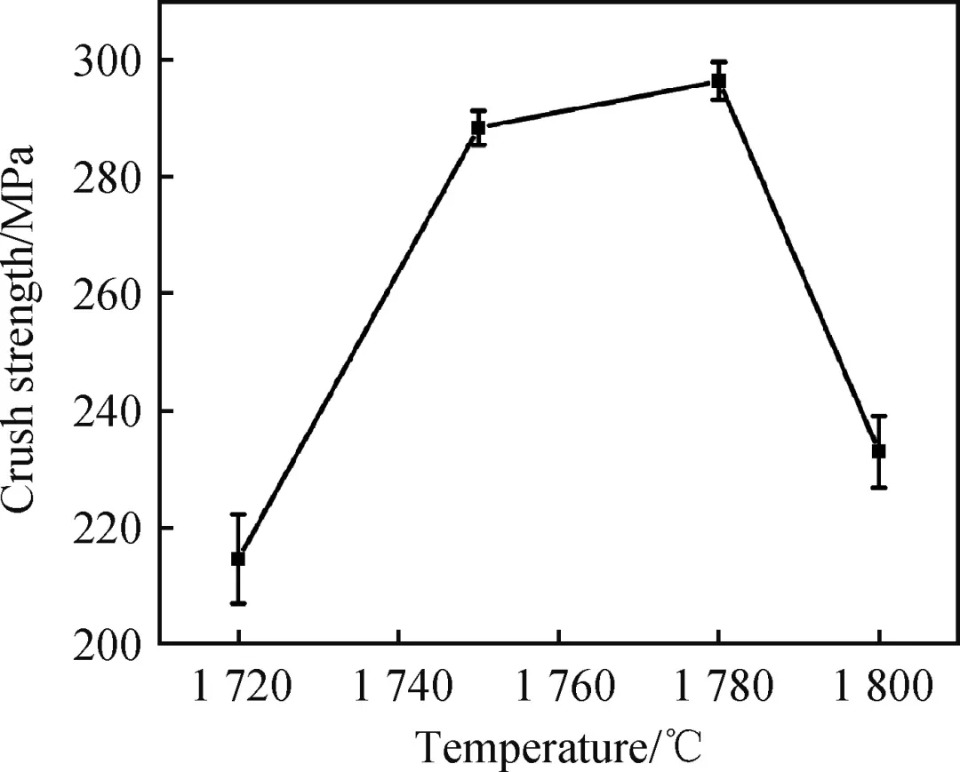
Fig.8 Effect of sintering temperature on crush strength of ceramic ball samples
Figure 8 shows the crushing strength and changes of ceramic ball samples at different sintering temperatures. As can be seen from FIG. 8, with the increase of sintering temperature, the crushing strength of ceramic ball first increases and then decreases. The crushing strength of ceramic ball is mainly affected by the density, microstructure and internal defects. The higher the density of ceramic ball, the more uniform the microstructure, the less internal defects and the higher the crushing strength. Among them, the crushing strength of ceramic balls sintered at 1750℃ and 1780℃ is higher, 288MPa and 296MPa respectively, indicating that the internal defects of ceramic balls sintered at these two temperatures are relatively few.
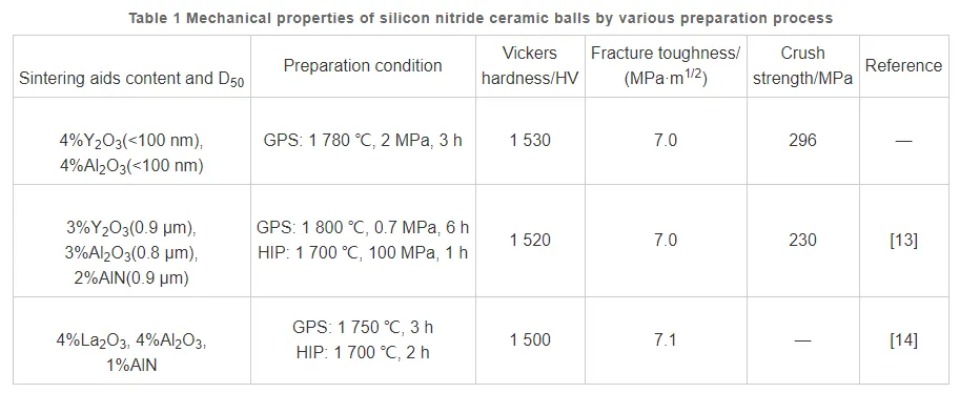
Table 1. Mechanical properties of silicon nitride ceramic balls by various preparation process
Table 1 shows the comparison of the properties of silicon nitride ceramic balls prepared by pneumatic sintering process and those prepared by hot isostatic pressing process abroad. It can be seen from Table 1 that the Vickers hardness and fracture toughness of the silicon nitride ceramic ball prepared in this test reach the same level as that of the foreign silicon nitride ceramic ball, and the crushing strength is higher than that of the foreign silicon nitride ceramic ball. Because the sintering agent used in this experiment is nano-scale, it can be more evenly dispersed in silicon nitride, promote the sintering densification of silicon nitride, improve the consistency of silicon nitride grain size, so the mechanical properties of the prepared ceramic balls are excellent.
Conclusion
In this paper, self-made α-Si3N4 powder was used as raw material and nano-scale Y2O3 and Al2O3 were used as sintering additives to carry out industrial experiments. The effects of sintering temperature on densification, phase composition, microstructure and mechanical properties of barometric sintering silicon nitride ceramic ball were studied. The following conclusions were obtained:
(1) With the increase of sintering temperature, the relative density of ceramic ball increases first and then decreases, and the grain size and length-diameter ratio increase gradually.
(2) The mechanical properties of silicon nitride ceramic balls are closely related to their microstructure, and the fracture toughness is mainly affected by grain size and length-diameter ratio. The fracture toughness increases with the increase of grain size and length-diameter ratio. Vickers hardness and crushing strength are not only affected by grain size, but also related to density and internal defects, so with the increase of sintering temperature, the trend of first increase and then decrease.
(3) The ceramic ball sintered at 1780℃ has the best comprehensive mechanical properties, its relative density reaches 99%, Vickers hardness, fracture toughness and crushing strength are 1530HV, 7MPa·m1/2 and 296MPa, respectively.