With the rapid development of power electronic technology, especially the wide application of power semiconductor devices such as high voltage, high current and high frequency IGBT modules, more stringent requirements are put forward for ceramic copper-covered substrates. As a kind of ceramic material with high thermal conductivity, low dielectric constant and good mechanical properties, aluminum nitride (AlN) is an ideal choice for preparing high performance ceramic copper-coated substrates. However, the surface properties of aluminum nitride substrate make it difficult for copper and copper oxides to wet and spread on it, limiting its direct application to DBC (direct bonded copper) processes. Therefore, to explore the efficient preparation process of aluminum nitride ceramic copper clad plate and optimize its performance has become the focus of current research.
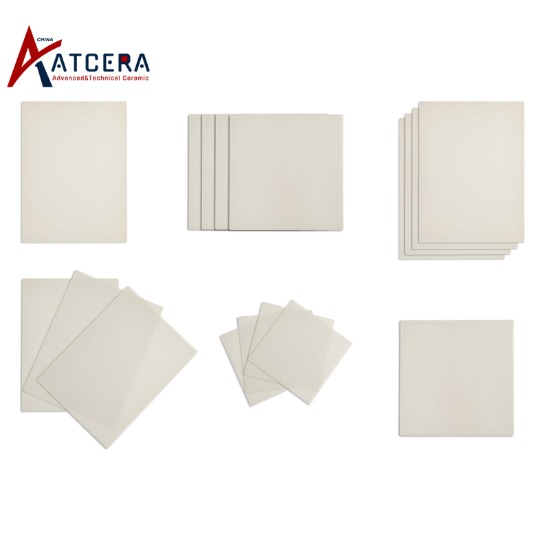
Challenges and solutions for the Aluminum nitride DBC preparation process: The surface properties of aluminum nitride make direct bonding with copper difficult. The wettability of copper and copper oxides on the surface of aluminum nitride can be significantly improved by forming a dense and uniform alumina composite layer on the surface of aluminum nitride. The DBC process uses the eutectic bonding of copper and alumina, and realizes the firm bonding of ceramic and copper foil through chain furnace sintering.
Introduction and advantages of the AMB process: As an improvement of the DBC process, the AMB (Active metal brazing) process uses the active element in the filler metal (such as Ti) to react with the ceramic to generate a reaction layer (such as TiN) that can be wetted by the liquid filler metal, thus enhancing the binding force of the ceramic and copper foil. The AMB process requires vacuum sintering to prevent oxidation of the active metal, and although the process complexity increases, the binding force is stronger and the reliability is higher.
Comparison of DBC and AMB process: The DBC process uses one step copper etching, while the AMB process consists of one step copper etching and one step TiN etching, the latter process is more difficult. However, the binding force of AMB-AlN is superior to that of DBC-AlN, showing higher reliability and performance.
Performance optimization direction of aluminum nitride ceramic copper-covered plate: With the development of power semiconductor devices, the performance requirements of ceramic copper-covered substrate are constantly improving. Improving the strength of aluminum nitride ceramics and further optimizing the preparation process to achieve higher reliability, temperature resistance and current carrying capacity are important directions of subsequent research.
To sum up, the preparation process of aluminum nitride ceramic copper clad plate has experienced the evolution from DBC to AMB, through the introduction of active metal brazing and vacuum sintering technology, effectively solve the problem of aluminum nitride surface wettability, significantly improve the bonding force and overall reliability of ceramics and copper foil. However, with the continuous progress of power semiconductor device technology, the performance requirements of ceramic copper-covered substrates are also increasing. Therefore, future research should focus on further optimizing the preparation process and improving the strength of aluminum nitride ceramics to meet the packaging needs of high-performance power semiconductor devices such as high voltage, high current and high frequency IGBT modules, and promote the sustainable development of power electronics technology.