In recent years, membrane separation technology has been widely studied and applied as one of the new technologies for sewage treatment. Compared with other technologies, such as gravity separation, coagulation, emulsion breaking, oil absorption and skimming, biodegradation, flocculation adsorption, ion exchange and other conventional separation processes, this technology has many advantages. Such as strong selectivity, low energy consumption, wide application range, environmental friendly, simple equipment, easy operation and so on. Oil-water separation membrane can be divided into organic membrane and inorganic membrane according to the material. Organic membrane has a wide range of applications in scientific research and commercial fields. Compared with organic membrane, inorganic ceramic membrane has strong chemical and thermal stability, excellent dirt resistance and pressure resistance, easy to clean, high mechanical strength, long life, so the use of ceramic membrane for oil-in-water emulsion separation is a major trend. Hydrophobic modification can enhance the wettability of ceramic film to oil, improve the separation efficiency of water-in-oil emulsion, and enhance the chemical stability and durability of ceramic film.
The form of water-in-oil (W/O) emulsion system is that water is dispersed in the oil in the form of small droplets. Membrane contamination during membrane separation leads to the decrease of permeation flux and retention rate with the extension of use time, which shortens the service life of the membrane and limits the application of membrane separation technology. The modification of the ceramic membrane surface can improve the specific selectivity and separation effect of the membrane, reduce the interaction between the membrane surface and unnecessary feeding molecules, and reduce the membrane pollution to a certain extent. Therefore, the separation of water-in-oil emulsions usually selects a hydrophobic film, which allows oil droplets to pass through and trap water droplets by using the hydrophobic and lipophilic characteristics of the membrane surface, so as to achieve the effect of oil-water separation.
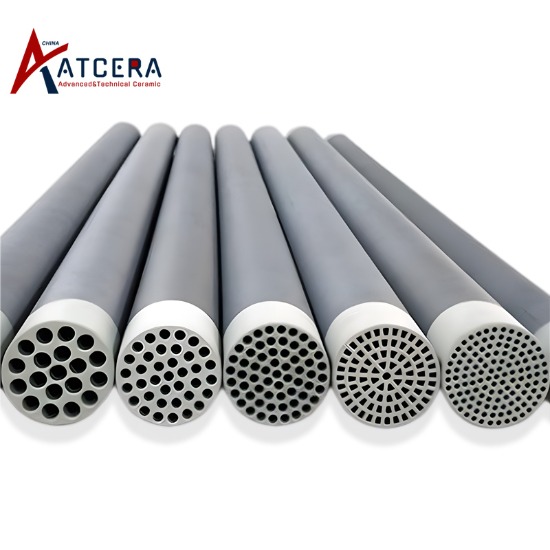
Hydrophobic modification of ceramic membrane surface
Hydrophobic modification of ceramic film surface is usually achieved by combining or adhering hydrophobic materials, selecting a lower surface energy, appropriate roughness and surface structure, such as the use of silane or thiol to provide surface chemical properties, and the introduction of micron or nanostructure to obtain a surface with better roughness, improve the hydrophobic effect of the film surface and enhance the separation performance.
There are three common methods for hydrophobic modification of ceramic membrane surface: impregnation, sol-gel and chemical vapor deposition.
01. Dip method
Impregnation method (Impregnation method) does not require special equipment, just the original ceramic film directly immersed in hydrophobic substance solution, the method is simple and direct, easy to operate, low cost. The hydrophobic modification of ceramic membrane surface is carried out by immersion method, which usually uses the functional group of hydrophobic substance to connect with the hydroxyl group on the ceramic membrane surface through condensation reaction.
Taking siloxane as a modifier for example, the operation steps of the impregnation method are as follows: dissolve the organosilane in water or ethanol and hydrolyze it to obtain a reactive silanol solution; When the pre-treated ceramic membrane is immersed in the solution, the reactive silane molecules can be adsorbed on the surface of the membrane, and the hydrophobic membrane can be obtained.
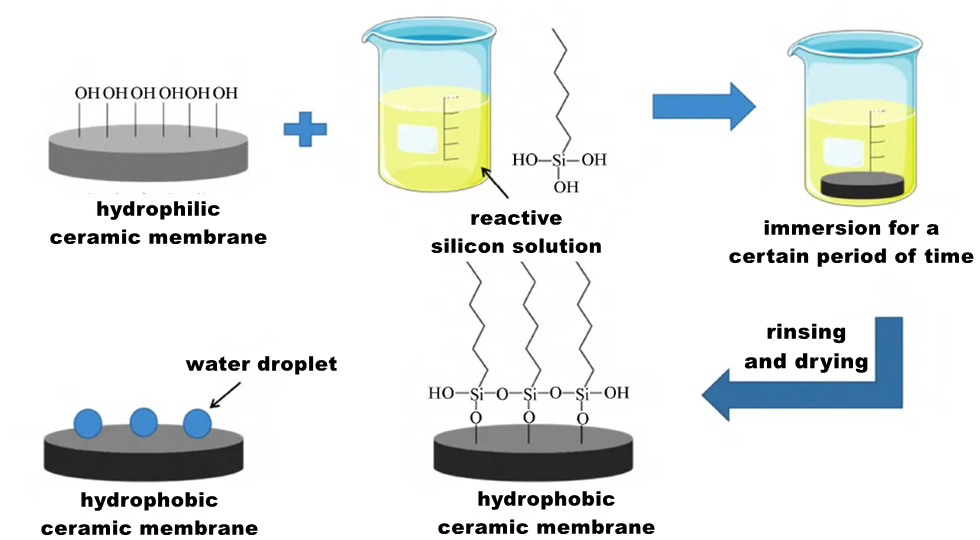
Hydrophobic effect is the result of the joint action of surface roughness and surface energy. In the study of hydrophobic modification of ceramic film, it is usually first to provide a certain rough micro-nano structure on the surface of ceramic film, and then modify it with low surface energy. In addition to the modification with silane coupling agent, mercaptan is also the preferred material to reduce the surface energy of the film.
In summary, the operation and steps of hydrophobic modification of the surface of ceramic film by impregnation method are relatively simple, and are greatly affected by the type of modifier, the concentration of modifier, the impregnation time, the number of impregnation times and the roughness of the surface of ceramic film. In addition, because the number of substances with low surface energy that react depends on its own concentration and the number of hydroxyl groups on the surface of ceramic film, Therefore, the method also has a great dependence on the reactive hydroxyl group on the surface of the ceramic membrane.
02. Sol-gel method
Sol-gel technique uses compounds containing highly chemically active components as precursors, and mixes these raw materials uniformly in the liquid phase. After chemical reactions such as hydrolysis and condensation, a stable transparent Sol system is formed in the solution. The sol is slowly polymerized among aged colloidal particles to form a gel with a three-dimensional network structure. The gel was dried and sintered to produce molecular and even nanostructured materials.
The hydrophobic modification of ceramic membrane by sol-gel method can form a large rough structure on the surface of the membrane, and can directly bind low surface energy chemicals. However, the early introduction of organosilane into the sol solution may lead to the formation of large volume polymers, resulting in poor modification effects.
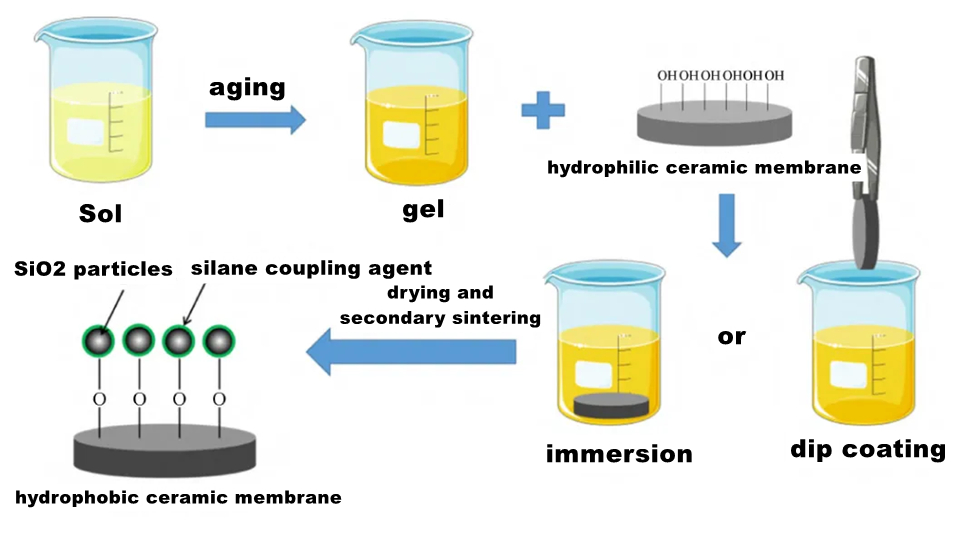
Compared with other methods, sol-gel method can prepare a stable hydrophobic surface with good separation effect, but it takes a long time to prepare the sol solution, and macromolecular polymers may be formed in the process, which affects the modification effect. In general, secondary sintering is required after the completion of coating, and the process is more complicated. In addition, excessive temperature during secondary sintering will destroy the structure of the film, reduce the hydrophobicity and stability of the film, and the aperture of the modified film will decrease with the increase of the number and time of sol-gel coating. In addition, the sol has an important effect on the formation of colloid in the process of colloid preparation, and then affects the film forming quality. Coating time and times, ambient temperature and humidity, heating rate, calcination temperature and calcination time all have a great influence on the subsequent coating drying process. At present, the process can be simplified by reducing the sintering steps at high temperature, forming a rough structure on the surface of the film at one time and combining with low surface energy materials, so as to reduce the damage of the film structure at high temperature.
03 Chemical vapor deposition method
chemical vapor deposition (CVD) uses gas phase reactants deposited on the substrate surface to form a solid film with specific chemical properties. The method has the advantages of controllable film composition, good film repeatability, uniform film layer, wide application range, no restriction on the shape of the substrate and no damage to the substrate material, and is an effective method to change the surface properties and microstructure of the film. For hydrophobic modification of the ceramic film using this method, the ceramic film needs to be placed in a closed container and heated at the boiling point temperature of the organosilane for a long time. The organosilane vapor is passed through to react with the hydroxyl group on the surface of the ceramic film, and the reaction principle is the same as that of the impregnation method.
Under normal circumstances, in order to make the organosilane reagent can be fully utilized, it is necessary to select a closed container with a size similar to the ceramic membrane, so that the contact and reaction of organosilane vapor with the ceramic membrane can be maximized.
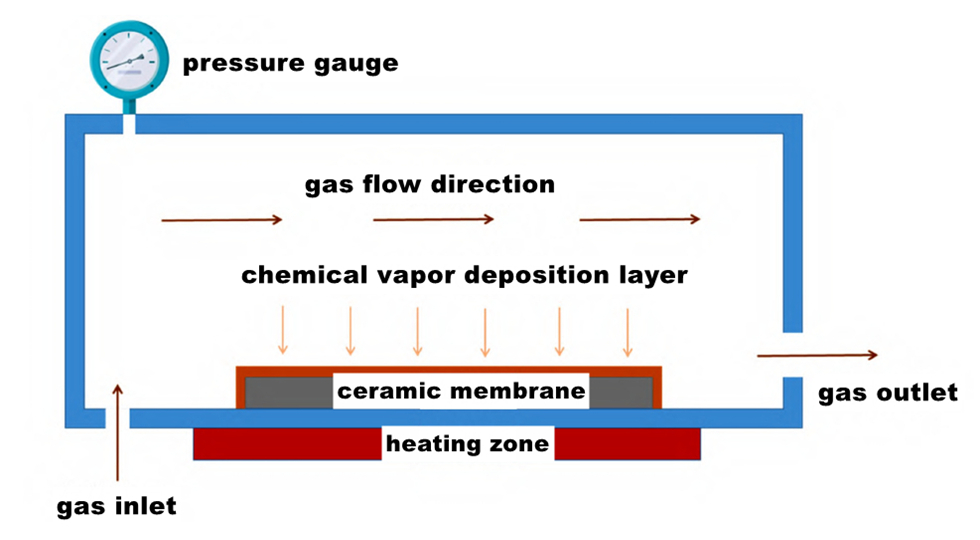
Chemical vapor deposition (CVD) is the preferred method to prepare micro-nano particles and nanorods on the surface of the film and form the ordered microstructure. The hydrophobic ceramic film modified by chemical vapor deposition has the advantages of uniform film layer, good stability and wide application range, but at the same time, the hydrophobic film thickness is thin, the mechanical properties are insufficient, and the defects such as cracks and bubbles are easy to occur under external impact. Water droplets and pollutants penetrate into the film through cracks, destroy its internal structure, and reduce the hydrophobic property and stability of the film. Some of the organosilanes involved in the deposition reaction are toxic and will cause harm to human body and environment. In addition, the reaction temperature required by this method is high, and the ensuing high energy consumption and high cost limit its application in actual industrial production.