Compared with other oxide ceramic membranes (alumina, titanium oxide, zirconia, etc.), silicon carbide membrane tube has higher hydrophilicity, permeability, pollution resistance and chemical stability. The sintering temperature of SIC ceramic membrane is closely related to the sintering technology, and the common sintering technology includes recrystallization technology, ceramic precursor conversion technology and in-situ reaction sintering technology.
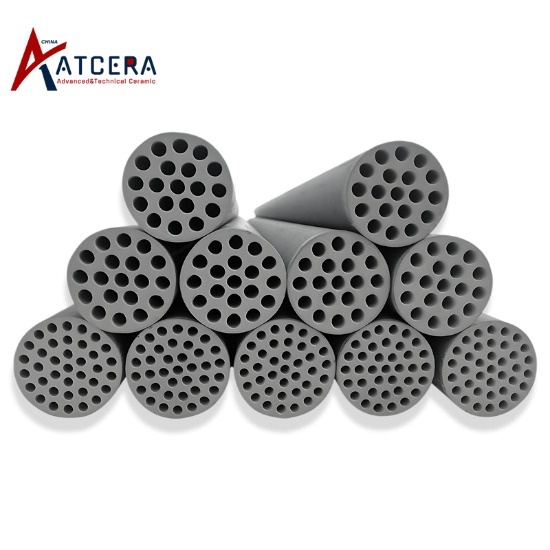
Recrystallization Sintering Technology
Recrystallization sintering technology refers to the realization of rejunction of SIC particles according to evaporation-condensation gas phase migration mechanism under high temperature sintering. This process does not involve too much chemical reaction, the pore size is greatly affected by the size of the raw material powder, the obtained silicon carbide membrane pore structure is uniform and the zigzag factor is low. Since silicon carbide has good stability in high temperature, high pressure and wide pH range, sintering additives and bipeak distribution of silicon carbide powder are generally used to reduce the sintering temperature during recrystallization. The silicon carbide membrane tube prepared by recrystallization sintering technology has high chemical stability, but its sintering temperature is high (> 1800℃), the energy consumption is large, and the inert atmosphere protection is required during the sintering process, and the equipment is extremely strict. In addition, in order to remove the possible residual carbon in the pore, after the completion of sintering, the surface oxidation needs to be carried out in an air atmosphere below 800 ° C, making the preparation process complicated.
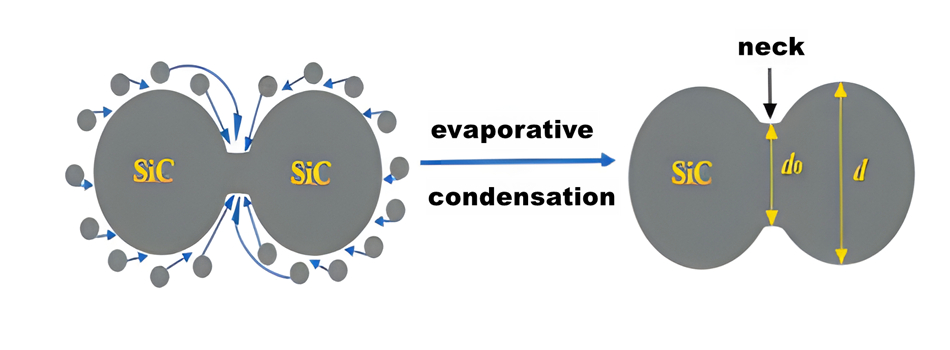
SiC high temperature recrystallization diagram
Ceramic Precursor Conversion Technology
The ceramic precursor conversion technology refers to the cracking of silicon-containing organic polymer (such as silicone resin, polycarbosilane, etc.) in an inert atmosphere and a certain temperature range (1100-1600℃) to form a bonding phase between silicon carbide aggregates, so as to prepare a c and a certain mechanical strength of silicon carbide ceramic membrane. The ceramic precursor conversion technology has low requirement on sintering temperature, which is conducive to reducing energy consumption. However, its raw material is high polymer, and the sintering process requires an anaerobic atmosphere, which has the disadvantages of high cost and complex process, which is not conducive to industrial production. In order to further develop and optimize the application potential of ceramic precursor conversion technology for membrane production, it is necessary to focus on cost reduction and microstructure regulation (pore size, porosity and membrane thickness).
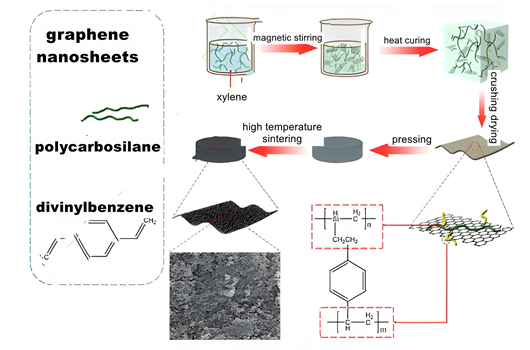
Preparation of silicon carbide ceramic membrane by ceramic precursor conversion technology
In Situ Reaction Sintering Technology
In situ reaction sintering technology refers to the addition of sintering additives to silicon carbide aggregate particles under an air atmosphere, so that it is much lower than the sintering temperature of pure phase silicon carbide ceramic membrane (1350-1550℃) to generate silicon oxide, and then the in-situ reaction with the sintering agent to form a neck connection. Common sintering additives are mainly metal oxides, such as alumina, yttrium oxide and zirconia. In the reaction process, mullite, cordierite and other multi-component oxides become the bonding phase of the neck connection between the particles. The addition of these sintering additives is conducive to the change of grain boundary and surface energy of SIC aggregate, thus accelerating the mass diffusion rate in the sintering process and reducing the sintering cost. In situ reactive sintering technology can effectively reduce the sintering temperature of SIC, but the process of membrane preparation still needs to be reduced.
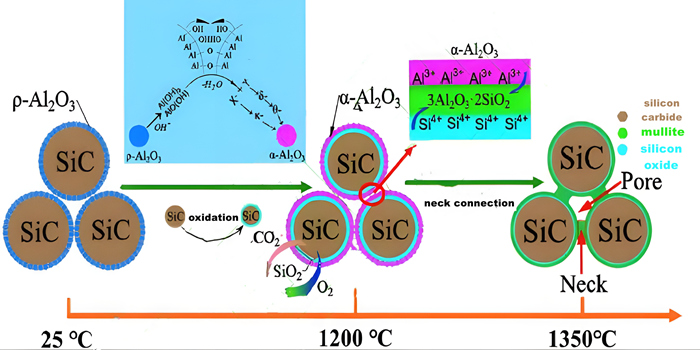
Schematic diagram of sintering process of mullite bonded porous silicon carbide ceramics prepared by in situ reactive sintering technique
In order to further improve the industrial application potential of silicon carbide membrane tube, it can be considered from the aspects of reducing cost and improving performance. For example, to reduce the cost, low-cost polymer precursors can be sought to prepare small pore size gas separation silicon carbide membranes; It can also optimize the combination of sintering additives, reduce the sintering temperature, and further expand the application range of co-sintering technology.
With the global concern for environmental protection, the demand for high-performance filtration and separation technology has become more and more urgent, which provides valuable opportunities for the development and application of silicon carbide membrane tube. In the future, a lot of resources are still needed to solve the problems of immature ceramic membrane production and preparation technology, so that the silicon carbide ceramic membrane separation technology can get more practical applications.