How to prepare high-performance silicon carbide membrane tubes for application process has become a research hotspot at present. Silicon carbide membrane is generally asymmetric structure, which is composed of support body, transition layer and separation layer. The preparation process mainly includes billet forming (supporting body forming, membrane forming) and sintering, both of which have a great impact on membrane forming performance. Appropriate preparation process can improve the integrity of ceramic membrane and prevent cracks, large holes and other defects. There are four main preparation methods for the membrane layer:
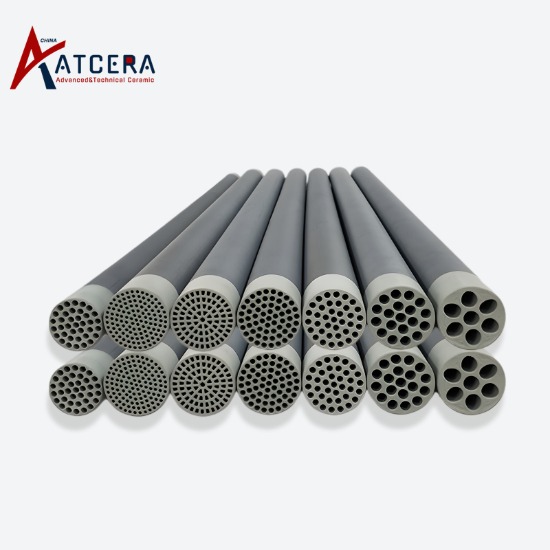
Dip Pulling Method
The dip and pull method mainly includes the following processes: Firstly, the ceramic particles or polymer precursors are dispersed in water or organic solvent to form a homogeneous and stable membrane making solution, and after coating, a wet membrane is formed on the surface of the porous support body. The membrane forming principle of this method includes "capillary filtration" and "membrane formation". Capillary filtration occurs when the dry porous support is in contact with the membrane-making solution. Under the capillary force, the dispersion medium enters the support body and the particles in the membrane-making solution stay on the surface of the support body to form a membrane. membrane formation occurs during the separation of the support body and the membrane-making solution after contact, and the membrane-making solution stays on the surface of the support body under the action of viscous force to form a membrane. The ceramic membrane tube after preparation and optimization has high repeatability and shows excellent effect in sewage treatment. Dip and pull method is one of the most widely used membrane preparation methods because of its simple operation and low energy consumption.
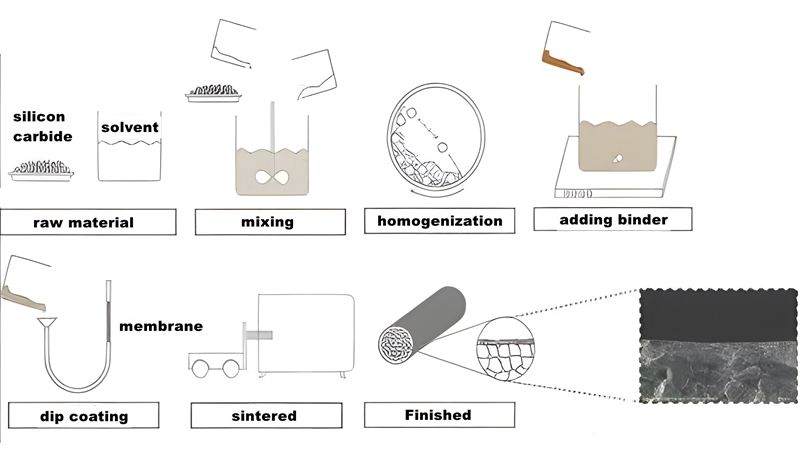
Step diagram of preparation of sic membrane by dip and pull method
Spraying Method
Spraying method is to use the spray gun to atomize the dispersed membrane making liquid into small droplets, and then deposit on the surface of the support body to form a membrane layer. The main operating parameters of the spraying method include the distance between the spray gun and the support body, the spraying pressure and the spraying time. Compared with dip and pull method, spraying method has the significant advantage of reducing the surface tension of the membrane making liquid through atomization, which is conducive to reducing the infiltration of the membrane layer into the support body pores, and thus reducing the interface resistance between the support body and the membrane layer. The spraying method has the advantages of easy large-scale production, simple operation, high slurry utilization efficiency and easy adjustment of membrane thickness. However, at present, this method is only used for the preparation of microfiltration membranes, and it does not meet the preparation requirements of small pore size membranes such as ultrafiltration and nanofiltration.
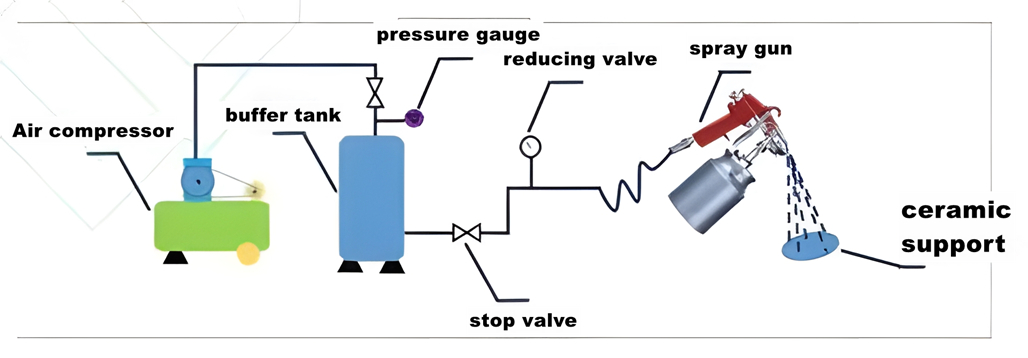
Spraying device diagram
Chemical Vapor Deposition Method
Chemical vapor deposition (CVD) is a method to prepare ceramic membrane by chemical reaction of one or several gaseous elements or compounds on the surface of porous support. The ceramic membrane prepared by this method has the characteristics of small membrane pore size and relatively low preparation temperature. However, CVD membrane has the disadvantages of harsh conditions, cumbersome process, high energy consumption and low membrane flux. At present, CVD membrane is mostly used in gas separation field, and its application in other fields needs to be further expanded. Chemical vapor deposition technology can only be used with chip ceramic membrane, and it is difficult to uniformly deposit in the preparation process of tubular or multi-channel ceramic membrane.
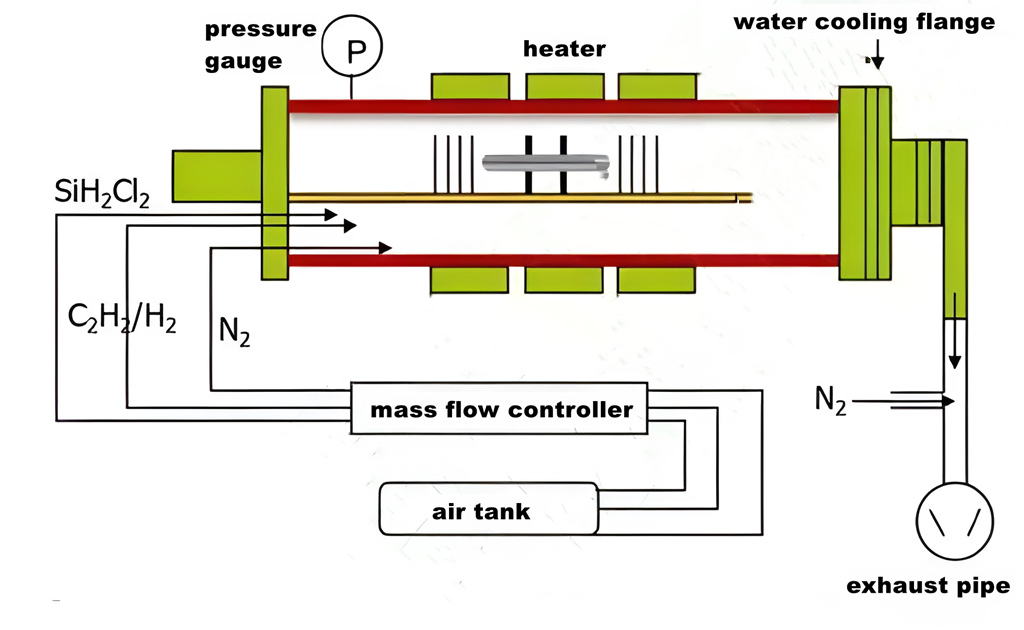
Schematic diagram of a CVD system for SiC membrane deposition
Phase Transformation Method
Phase conversion means that ceramic paste containing a large amount of polymer solution can be changed from liquid to solid by wet or dry induction, wet and dry means that the polymer solution is exposed to a non-solvent condensation bath or atmosphere. During the phase transformation process, the polymer morphology is retained as ceramic membrane pores, which are usually divided into finger pores and spongy pores, and have relatively low porosity factor, which is conducive to the preparation of higher flux ceramic membranes. The porosity of the traditional ceramic membrane is between 25.95% and 47.64%, and the porosity of the ceramic membrane prepared by the phase transformation method is more than 70%. However, the poor mechanical stability and brittleness of the samples prepared by this method limit its application in industry. The phase transformation method is an effective way to prepare ceramic membrane with hierarchical porous structure in one step, which has a wide application prospect for optimizing the structure of ceramic membrane and increasing the porosity and flux of ceramic membrane.
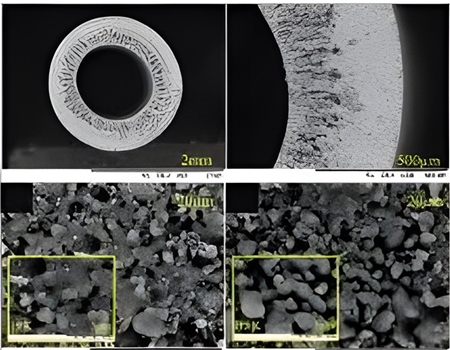
Pore size distribution and SEM image of SIC hollow fiber membrane before and after surface modification