In the rapidly evolving world of industrial technology, zirconia valves have emerged as a pivotal component in the field of advanced technical ceramics. These valves, owing to their superior performance characteristics, have garnered significant interest among engineers and operators across Europe and the Americas. This article delves into the intricacies of zirconia valves, exploring their unique properties, applications, and selection criteria, with a focus on how they can be tailored to address the specific needs of today's industrial landscapes.
Characteristics of Zirconia Valves
Zirconia, a high-purity material with excellent corrosion resistance, is a game-changer in the world of ceramic valves. Its unique chemical stability ensures that zirconia valves can withstand a wide range of corrosive liquids without contaminating the fluid. Moreover, zirconia's high processing precision allows for precise flow control, making it an ideal choice for applications requiring stringent accuracy. The sealing surface of zirconia valves boasts remarkable smoothness and self-lubrication, resulting in superior sealing performance and reduced wear.
Application Fields of Zirconia Valves
The versatility of zirconium oxide valves is reflected in their diverse application fields. They find extensive use in machinery equipment, petrochemical plants, pharmaceutical and biotechnology industries, food processing units, power plants, water supply systems, and metal smelting facilities. Their corrosion-resistant properties and precision control make them indispensable in these environments, where reliability and durability are paramount.
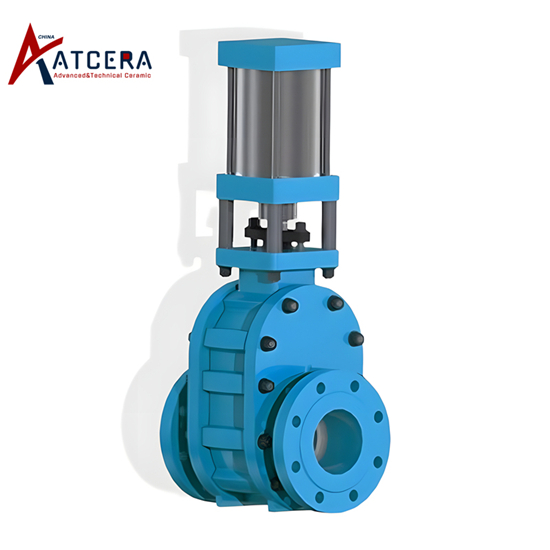
How to Select the Right Zirconia Valve for Your Project
Choosing the right zirconia ceramic lined valve for a specific project requires a thorough understanding of the application's requirements. Key considerations include the type of fluid to be handled, the desired flow rate and accuracy, as well as the operating conditions such as temperature and pressure. Additionally, the valve's material compatibility, sealing performance, and durability should be carefully evaluated to ensure it meets the project's long-term needs.
Manufacturing Process of Zirconia Valves
The manufacturing process of zirconia valves is a testament to the precision and rigor of advanced technical ceramics. High-purity zirconia powder is carefully selected and processed using sophisticated techniques to achieve the desired material properties. The valves are then precisely crafted using advanced machining and finishing methods, ensuring optimal performance and durability.
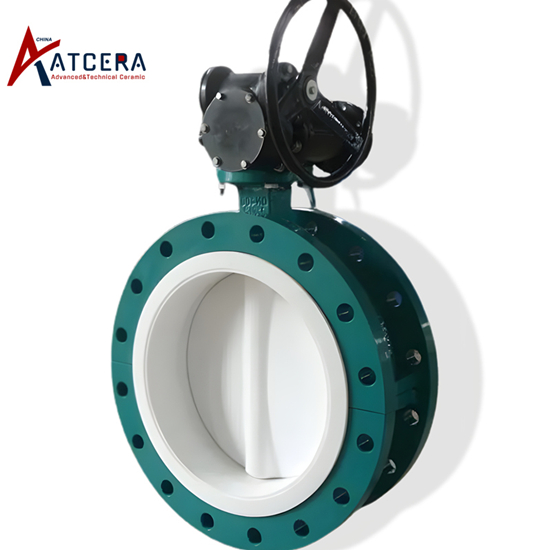
Case Studies and Success Stories of Using Zirconia Valves
Numerous case studies and success stories have highlighted the benefits of ZrO2 valves in various industrial applications. From petrochemical plants where they withstand harsh chemicals, to food processing units where they ensure purity and safety, zirconia valves have proven their worth in demanding environments. These real-world examples demonstrate the reliability and effectiveness of zirconia valves in addressing the specific challenges faced by today's industries.
Conclusion
Zirconia valves, as a key component in advanced technical ceramics, have revolutionized fluid control in industrial applications. Their superior corrosion resistance, precision flow control, and exceptional sealing performance have made them an indispensable choice for engineers and operators across Europe and the Americas. As the industrial landscape continues to evolve, zirconia valves will remain at the forefront of innovation, addressing the evolving needs of today's demanding industries.